What Is Reverse Logistics in Supply Chain Management?
What is reverse logistics? For logistics, we often talk about how goods move from manufacturers to customers. However, there is another form of logistics that involves products moving from those destinations back to warehouses and manufacturers. Read on to learn more about what reverse logistics entails.
WHAT IS REVERSE LOGISTICS IN SUPPLY CHAIN MANAGEMENT?
When customers are unsatisfied with a product, they may contact the company for a refund or a replacement shipment. Yet what happens with the product? Some companies request for it to be sent back to them for evaluation and possible disposal. The reclaiming of this product — from sending packaging for its return, delivery trucks picking it up, receiving it at the warehouse, and planning on the product’s disposal, or recycling and salvaging parts — is considered reverse logistics. It’s the strategies that companies implement to receive an existing product from the customer to regain value from it.
Keep in mind that reverse logistics expands beyond simply reclaiming damaged or unwanted products from customers. It may also involve reclaiming packaging materials as well as old items that have reached the end of the product lifecycles. Companies may also provide reverse logistics for old products when a customer upgrades to a newer version of the same product, such as a phone recycling program where people can return their old devices.
Reverse logistics not only involves retrieving goods from customers. B2B reverse logistics may consist of a company obtaining raw materials or items that are no longer needed. For example, a food processor may obtain empty bottles; containers; or pallets from restaurants, hospitals, or schools that may be sanitized and reused for the next food shipment.
The process of reverse logistics proceeds as follows:
- Processing returns: The first step in the process focuses on the reason for the return. The company gathers this important data to determine what will occur to the product once it begins its reverse journey back to the seller, warehouse, or even supplier. You may also authorize the client to return the product and provide remediation, such as issuing a return or product replacement in certain circumstances.
- Shipping products: How the product returns through the supply chain will depend on the seller’s policies. You may have the customer take on shipping costs or provide packaging for the shipment to be returned. Other times, you may have drivers available to retrieve the products based on the location of the product in relation to the distance to the warehouse or distribution center.
- Evaluating products for further processing: A fully optimized supply chain will already know where the products are headed before leaving the customer. Yet if your processes are not this advanced or you have smaller operations, you may have a process where products are evaluated at distribution centers or warehouses to determine their next step for processing. During this stage, the product may be reviewed for damage or any other issues.
- Restocking, repairing, recycling, remanufacturing, or disposing: The workers gather data regarding the condition of the products and then send the products to their next destinations. This step may involve the product being sent back to the warehouse for restocking or to a reaper facility so that it may be refurbished and resold.
Some products that have reached their end cycles and contain dangerous materials that should not re-enter the environment may go through special disposal operations. Another possible option involves your company recycling the product for parts to be used in other products, or remanufacturing the product with upgraded technology.
Implementing these processes requires understanding a key factor: What does reverse logistics mean for your company? It means knowing the type of reverse logistics you want to offer with customers or implement at a specific time during the product’s life span. If your company requires end-of-life, packaging management, delivery failures, and unsold goods, you require a supply chain versatile to handle the product return streams.
Having a 3PL operate your reverse logistics takes the work out of your hands. A 3PL may operate your fulfillment, distribution, warehousing, and customer service processes. It will have first contact with a customer seeking to return a product.
Then, a 3PL can send the product through the appropriate channel for it to be reused, restocked, recycled, or refurbished. With its versatility, scalability, and expertise, a 3PL may oversee this part of the supply chain so you can focus your time and effort on gaining new customers.
Benefits of Reverse Logistics
- Gaining valuable product data: A company cannot know if there is a serious issue with a product if customers do not return it. Having reverse logistics and a comprehensive return policy allows you to collect important data about the product so issues can become rectified by the supplier.
- Potential increased revenue: Product returns focused on recycling, reusing, or remanufacturing the existing products may create additional revenue for the company. Obtaining the previous product may save on material costs to remake the product when the existing one can be placed back into use.
- Waste reduction: Reverse logistics may lower the number of products and packaging tossed into landfills. It might also prevent customers from dropping dangerous materials straight into the garbage. Instead, the appropriate disposal can be taken by the company.
- Cost reduction: Retrieving products may create short-term and long-term cost savings. You’re able to receive packaging, pallets, and containers that may immediately be placed back into use. You also learn about possible supply chain issues that could cause customer dissatisfaction, as your company may proactively address the supplier or transportation issues.
- Good company branding: A comprehensive and transparent return process combined with efficient reverse logistic processes creates positive outcomes for customers. Even when receiving damaged or malfunctioning products, customers may still work with a company that handles their returns professionally. In addition, you might offer branding opportunities that show how your company cares about reducing waste to the environment or offers discounts when returning products.
Industries That Benefit from Reverse Logistics
Typically, any industry offering products directly to consumers or other companies may have return policies and reverse logistic procedures. Some common ones can include:
- Electronics
- Apparel
- Retail
- Food and beverage
- Construction
- Pharmaceutical
- Automotive
WSI for Reverse Logistics Services
Due to the possible complexity of reverse logistics, you may outsource the task to other companies that are focused on providing reliable and experienced logistical strategies based on your industry. You could then tap into their wealth of resources and technologies to reclaim products at the appropriate time while still maintaining satisfied customers. For some companies, they might have a 3PL focused entirely on offering reverse logistic services. Other companies may have the 3PL handle warehousing, distribution, order fulfillment, and reverse logistics so they gain a comprehensive logistics solution handled by a single 3PL partner.
Here at WSI, we provide outsourced logistics solutions to a range of industries for businesses. We offer contract logistics as we tailor our work to reflect the current and future needs of your operations, scaling our solutions to match your operational capacity. In addition to offering logistical solutions for order fulfillment, warehousing, and distribution processes, we provide reverse logistic services.
Contact WSI to learn more about the types of reverse logistics that would be the most appropriate for your supply chain.
About the Author
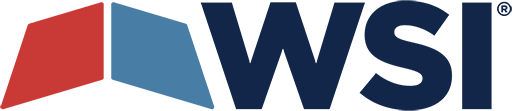
WSI Team
WSI is one of the largest privately held 3rd party logistics companies in the U.S. and spans a nationwide distribution network with global logistics reach.