Why Fulfillment Location Matters, And When It Doesn’t
It’s true: Location matters in fulfillment and when choosing a 3PL partner. However, the final decision is more nuanced. While the area and proximity to customers, transportation infrastructure, and labor should factor heavily into where to place logistics operations, it’s not the only thing businesses need to think about.
Yes, companies should look for 3PL providers near their customer hubs or manufacturing facilities. They need to be located near ports, highways, airports, and railroads. The chosen area should provide sufficient labor, be cost-effective, and facilitate meeting regulatory requirements. Yet the warehousing and fulfillment location chosen should also have the right capabilities to support your product and material storage needs.
This article examines how location impacts fulfillment efficiency, why capabilities often outweigh zip codes, and how to assess fulfillment centers based on both geography and specialty.
The strategic value of fulfillment location
Fulfillment location affects a host of things. The region that businesses choose is defined by proximity to distribution hubs and placement near major highways, ports, railroads, and airports.
For example, the West Coast region, especially areas near Los Angeles, places companies within a vast logistics network and major Asian import hub. Additionally, it typically offers competitive labor rates and provides a buffer against disruptions, such as extreme weather. But before deciding on the West Coast, there are other things businesses would likely consider.
Fulfillment location is beneficial when it:
- Places products near customers, reducing shipping time and cost, especially as rates continue to grow.
- Provides a strong labor pool. Some areas have better warehouse labor markets
- Has an established transportation network with optimal routing and delivery paths.
- Supports flexibility and scalability, allowing retailers to easily expand operations.
The role of fulfillment location in logistics operations
Location is central to operational efficiency, cost-effectiveness, and reliable services. Think of it like this: When you’re positioned near your end customers or high-demand hubs, it immediately increases shipping speeds and lowers costs. At a time when consumers want products delivered fast and free, this helps retailers meet rising expectations.
By strategically storing and distributing inventory across multiple locations, businesses can optimize stock availability while improving coverage and maintaining ideal stock levels for various channels. And when a fulfillment center is well-placed, it also streamlines reverse logistics and returns management processes.
Another role of location is placing businesses strategically in areas that support compliance. For example, certain states have stricter rules for labor, specialized storage, or zoning, which is why it’s beneficial to select a storage and fulfillment location that aligns with your product type and industry requirements while helping avoid costly disruptions due to regional regulations and compliance.
When location alone isn’t enough (and why capabilities matter)
When retailers set out to choose a 3PL location, they must balance proximity with performance. In other words, finding a 3PL warehousing and fulfillment provider that is not only optimally located but able to handle any unique storage and distribution needs. It’s easy for brands to over-prioritize zip code without assessing warehouse capabilities.
A poorly equipped facility in a “perfect” location can disrupt operations. When selectin a 3PL provider, move beyond location and look at:
- Technology: Does the 3PL offer modern technology that supports omnichannel operations, real-time order and inventory management, automated order processing, and data-driven insights? Look at how the provided WMS and integrations function and if they work with your existing retail tech stack.
- Safety protocols and certifications: Certifications and safety may not be the first things businesses look at, but they are a critical part of selecting a 3PL partner and fulfillment location. This becomes more important when businesses have specialty products, such as chemicals, paper, big and bulky, supplements, or food and beverage.
- Storage capabilities: When searching for a fulfillment location, businesses must assess their storage needs. This includes product size, weight, turnover rate, handling requirements (e.g., fragility, temperature control, and hazardous materials), and factors like SKU count for warehouse layout and storage methods (bins, pallets, shelves). Retailers should also consider any specialized racking or equipment that may be required.
- Value-added services (VAS): VAS helps businesses differentiate and improve the customer experience. Retailers should look at whether a location offers things such as kitting, packaging, or assembly services.
Assessing these needs enables companies to find a 3PL that fulfills both location and capability requirements.
Finding a warehouse or fulfillment center that matches your industry needs
It’s not a surprise that different industries have different needs. However, it’s more extensive than businesses might think. Consider this: Chemicals require specialized handling, and transport must comply with hazmat regulations, storage needs ventilation, spill containment, and fire suppression systems, and distribution often involves strict labeling and documentation.
In contrast, apparel transport is more flexible, storage prioritizes clean, climate-controlled environments to prevent damage, and distribution focuses on high SKU variety, fast picking, and returns processing. While both an apparel and chemical retailer might want to be in the same area to be near customers, they’ll need distinct fulfillment locations and centers that best support their operations.
Companies must look at the required infrastructure, safety, and compliance standards needed to store and fulfill their products. Here are some examples of what specific industries might look for:
Industry | Key fulfillment needs |
Manufacturing | Bulk storage, cross-docking capabilities, light assembly or kitting |
Chemicals | Hazmat handling, proper ventilation, spill containment, regulatory compliance |
Paper & printing | Clean, dry environments, controlled humidity, specialized stacking and storage solutions |
Retail | Fast and accurate picking and packing, high-volume order processing, efficient returns handling |
Food & Beverage | Temperature-controlled zones, health and safety compliance, FIFO and FEFO inventory management |
For businesses with products that are highly regulated, specialized, or require specific handling, niche-focused facilities often offer greater operational efficiency than generalized ones.
Why choose regional fulfillment over pinpoint location
It’s not uncommon for businesses to seek warehouses and fulfillment centers near their headquarters or in a specific city. However, regional proximity suffices and may even offer more benefits. A regional hub will often cover multiple states or zones and still reduce transportation costs and improve scalability. Centralizing location (especially if there is only one) supports omnichannel distribution more effectively. As a business grows, they can look to multiple locations, wider networks, and still aim to choose areas that offer cost-effectiveness and flexibility.
Location matters, but it’s not everything. The best warehousing and fulfillment solution balances location, capability, and industry alignment. It’s essential to look beyond the map and assess 3PL providers by what they can do, not just where they are. If you’re looking for a logistics partner that checks all the right boxes, including fulfillment location, capability, and industry expertise, talk to one of our experts today and discover the best-fit solution for your business.
A Sample of WSI’s Warehousing and Fulfillment Locations and Capabilities
Location | Key Capabilities & Specialties | Transportation Access | Industries Served |
Columbus, OH | General warehousing; transportation; fulfillment; FDA-registered | CMH (John Glenn Columbus), 0.25 mi north; LCK (Rickenbacker), 15 mi south; Port of Cleveland, 150 mi north; I-70, 5 mi south; I-270, 2 mi east | Furniture & Home Goods, Sporting & Outdoor, Equipment & Industrial, Food & Beverage, Pet Products, Building Material, Chemicals. Apparel, Beauty, Electronics, Paper, Consumer Products |
Sauk Village, IL | Warehousing; chemical warehousing; transportation; fulfillment | MDW (Midway), 22 mi north; ORD (O’Hare), 38 mi north; access to rail; Port of Indiana, 27 mi east; Illinois International Port District, 20 miles north; I-70, 7 mi north; I-57, 8 mi west; I-65, 13 mi east | Furniture & Home Goods, Sporting & Outdoor, Equipment & Industrial, Food & Beverage, Pet Products, Building Materials, Chemicals, Apparel, Beauty, Electronics, Paper, Consumer Products |
Allentown, PA | Warehousing; transportation; chemical storage | ABE (Lehigh Valley International), 12 mi east; NS Allentown Terminal (rail), 12 mi east; Port of Philadelphia, 60 mi south; Port of New York, 110 mi east; I-78, 0.5 mi south; I-476, 2 mi west | Furniture & Home Goods, Sporting & Outdoor, Equipment & Industrial, Food & Beverage, Pet Products, Building Material, Chemicals, Apparel, Beauty, Electronics, Paper, Consumer Products |
Pomona, CA | Warehousing; transportation; chemical storage | ONT (Ontario), 11 mi east; LAX, 48 mi west; Port of Los Angeles/Long Beach, 45 mi west; I-10, 2 mi south; I-210, 2 mi north; BNSF, 17 mi west | Furniture & Home Goods, Sporting & Outdoor, Equipment & Industrial, Food & Beverage, Pet Products, Building Material, Chemicals, Apparel, Beauty, Electronics, Paper, Consumer Products |
Fontana, CA | Warehousing; transportation; fulfillment | ONT (Ontario), 9.4 mi west; LAX, 63 mi west; Port of Los Angeles/Long Beach, 63 mi west; I-15, 3 mi west; I-10, 2 mi south; CA-60, 6.5 mi south | Furniture & Home Goods, Sporting & Outdoor, Food & Beverage, Pet Products, Apparel, Beauty, Electronics, Paper, Consumer Products |
Garland, TX | Warehousing; transportation; fulfillment; chemical warehousing | DFW (Dallas/Fort Worth), 20 mi west; UP, Wilmer (container yard), 26 mi south; BNSF, Haslet (container yard), 48 mi southeast; Port of Houston, 250 mi south; I-635, 0.5 mi | Furniture & Home Goods, Sporting & Outdoor, Equipment & Industrial, Food & Beverage, Pet Products, Building Material, Chemicals, Apparel, Beauty, Electronics, Paper, Consumer Products |
Visit our location page to see all our facilities.
About the Author
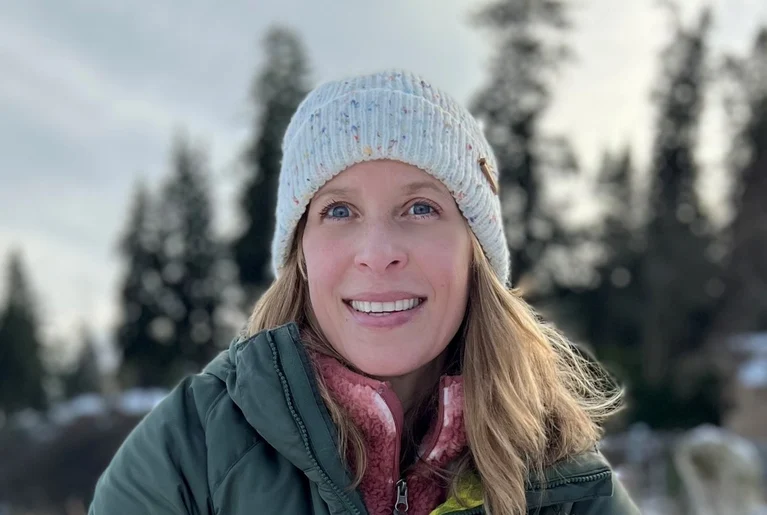
Alyssa Wolfe
Alyssa Wolfe is a content strategist, storyteller, and creative and content lead with over a decade of experience shaping brand narratives across industries including retail, travel, logistics, fintech, SaaS, B2C, and B2B services. She specializes in turning complex ideas into clear, human-centered content that connects, informs, and inspires. With a background in journalism, marketing, and digital strategy, Alyssa brings a sharp editorial eye and a collaborative spirit to every project. Her work spans thought leadership, executive ghostwriting, brand messaging, and educational content—all grounded in a deep understanding of audience needs and business goals. Alyssa is passionate about the power of language to drive clarity and change, and she believes the best content not only tells a story, but builds trust and sparks action.