Warehousing in California: What Businesses Need To Know
California is one of the most vital logistics gateways in the United States. The Ports of Los Angeles and Long Beach alone handles 31% of all U.S. container imports, while the state’s highways and intermodal hubs connect supply chains from Asia to the rest of North America. Despite its advantages, California presents a complex environment for businesses warehousing in California and shipping and storing goods.
From evolving environmental regulations to stringent fire codes and permitting requirements, operating within the state demands careful planning and compliance. Before investing in warehouse space or expanding logistics operations in California, it’s crucial to understand the full scope of regulatory and operational considerations.
Considerations for businesses shipping and storing in California
Environmental and safety regulations are among the strictest in the country for storage, fulfillment, and warehousing in California. For businesses shipping and storing goods within the state, compliance is critical. Below are key regulations that affect warehouse operations and logistics planning.
WAIRE Program (Warehouse Actions and Investments to Reduce Emissions)
The WAIRE Program focuses on reducing emissions from warehouse operations, particularly those related to truck traffic. Warehouses 100,000 square feet or larger in Los Angeles, Orange, Riverside, and San Bernardino counties are required to comply with the WAIRE Program.
Facilities are required to track truck visits and earn “WAIRE Points” through zero-emission investments such as electric vehicle infrastructure or solar installations. Non-compliance can result in $1,000 per point mitigation fees, with penalties that can reach six figures.
CARB Transportation Regulations
The California Air Resources Board (CARB) has implemented several rules aimed at reducing emissions from vehicles, particularly heavy-duty trucks and buses, to improve air quality and protect public health. The current CARB regulations include:
- Truck and Bus Regulation: Heavy-duty trucks are required to meet strict emissions standards.
- At-Berth Regulation: Tanker and Ro-Ro vessels must use emissions control strategies at California ports. (effective January 2025)
- Transport Refrigeration Unit (TRU) Rule: All TRUs must transition to zero emissions by 2029.
- Advanced Clean Trucks (ACT) Rule: Manufacturers are required to increase sales of zero-emission vehicles, which will impact fleet availability and planning.
Chemical storage and hazmat requirements for storage, fulfillment, and warehousing in California
Facilities that store chemicals and hazardous materials are subject to stringent compliance obligations. These regulations exist to protect public safety, worker health, and the environment from improper storage or handling that can lead to fires, explosions, toxic exposure, or environmental contamination.
These rules also ensure facilities are secure from theft or misuse of hazardous substances and provide emergency responders with the necessary safety information. Compliance helps prevent accidents, reduces liability, and supports safe, sustainable operations.
In California, warehouses storing hazardous materials (HAZMAT) are required to secure an annual Fire Department permit. The permit application process involves submitting a Hazardous Materials Business Plan (HMBP) for review and approval by the local fire department. The HMBP outlines how the hazardous materials will be safely stored and handled.
Warehouses storing chemicals must also comply with Chemical Facility Anti-Terrorism Standards (CFATS), ensuring DHS security compliance for high-risk facilities. Managed by the Cybersecurity and Infrastructure Security Agency (CISA), CFATS is intended to reduce the risk of dangerous chemical use in terrorist attacks by requiring facilities to implement security measures.
Adhering to Segregation Requirements by storing different chemical classes in separate, marked areas is a crucial safety measure. Incompatible chemicals can react violently when mixed, potentially leading to fires, explosions, or the release of toxic fumes. Segregating chemicals based on their class and reactivity minimizes the risk of these dangerous reactions.
Proposition 65 (Chemical Labeling Requirements)
Recent changes to California’s Proposition 65, effective January 1, 2025, require short-form warnings to include the names of specific listed chemicals, with full compliance required by 2028. This regulation applies to nearly 900 substances known to cause cancer or reproductive harm. Penalties can reach up to $2,500 per violation, per day—even for inadvertent exposures.
California Fire Code Compliance
Warehouse operators must meet strict fire code standards, particularly for high-piled storage and flammable materials. Facilities storing items over 12 feet high require annual permits and specialized sprinkler systems. Flammable liquid storage is subject to strict quantity limits and fire suppression rules. Clear aisles, emergency egress, and proper sprinkler coverage are non-negotiable for compliance.
Supply Chain Transparency Act (SB 657)
SB 657 requires businesses with over $100 million in annual gross receipts doing business in California to publicly disclose their efforts to prevent human trafficking and slavery in their supply chains. This requirement underscores the state’s emphasis on ethical sourcing and labor transparency for any businesses fulfilling or warehousing in California.
Why a 3PL partnership makes sense in California
Given the complexity of California’s logistics environment and warehousing in California, many businesses opt to partner with a third-party logistics (3PL) provider to mitigate risk, ensure compliance, and maintain focus on their core operations. Regulatory requirements, such as WAIRE tracking, CARB compliance, chemical permitting, and Prop 65 labeling, all require deep expertise, established infrastructure, and consistent oversight, capabilities that many internal logistics teams are not equipped to manage independently.
An experienced 3PL with a California footprint can offer:
- Regulatory expertise and readiness: From emission-reduction documentation to fire code inspections, a 3PL can ensure you stay compliant without tying up your internal resources.
- Permitted, audit-ready facilities: Leading 3PLs already operate warehouses with the appropriate fire and hazmat permits, saving you the time and cost of building compliance from scratch.
- Scalable, resilient operations: Whether you’re moving construction materials, chemicals, or temperature-sensitive products, a California-based 3PL can provide flexible solutions that align with regulatory thresholds and operational needs.
- Reduced legal and reputational risk: Non-compliance doesn’t just cost money—it can damage relationships with customers, regulators, and local communities.
As Mike Venditti, VP of Fulfillment Operations at WSI/Kase, explains:
“Navigating California’s environmental landscape can be a drain on internal resources. Non-compliance in California carries steep fines and reputational risk. Our established processes, trained staff, and track record with audits and inspections ensure a lower risk profile for your brand when operating in this challenging environment.”
By choosing a partner like WSI, shippers gain access to the infrastructure, expertise, and compliance support needed to succeed in California’s highly regulated logistics market.
Prepare for California Warehousing Success
California remains a key logistics hub and an excellent fulfillment location, despite being one of the most challenging states for warehousing and distribution due to its layered regulatory environment. Ranging from air quality mandates and hazardous material rules to fire code compliance and supply chain transparency laws, businesses must approach operations in the state with diligence and a clear strategy.
A knowledgeable 3PL partner like WSI can help you navigate these challenges, avoid costly mistakes, and keep your supply chain running smoothly. If you’re shipping goods or warehousing in California, ensure your logistics strategy is prepared for both the risks and rewards this market presents. Don’t let California’s regulations catch your business off guard. Talk to a logistics expert today to safeguard your operations and simplify compliance.
About the Author
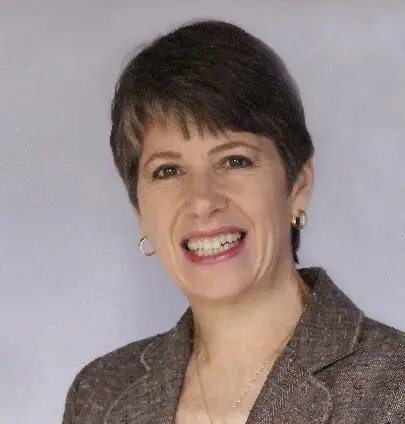
Margot Howard
Margot Howard is a Freelance content marketing writer and strategist with 10+ years of experience. Margot worked in corporate sales for many years before transitioning to content marketing. She writes for B2B SaaS, software, and service companies, especially those in shipping and logistics, Sales Tech, and MarTech.