Order Picking: How to Leverage Technology and Productivity to Improve Order Fulfillment
AS DIGITAL TECHNOLOGIES CONTINUE TO GROW, IT’S BECOME INCREASINGLY IMPORTANT FOR BUSINESSES TO MODERNIZE THEIR ORDER PICKING WORKFLOWS. BUT AS COMPANIES PIVOT TO MEET THE GROWING DEMANDS OF CONSUMERS, WHERE DO YOU BEGIN? HERE’S A LOOK AT HOW TECHNOLOGY AND IMPROVED PRODUCTIVITY CAN LEAD TO OPTIMAL FULFILLMENT.
We have all been affected by the Amazon effect. The Ecommerce giant changed shopping patterns, customer expectations, and the industry’s competitive landscape. Couple those expectations with a global pandemic and supply chains are feeling the disruptions from order to delivery.
This is where having a strategic location for your warehouse, like our Dallas fulfillment center, can make a significant difference.
Supply chains have had to adapt to these new expectations, integrating digital technologies to become more efficient and streamlined. Warehouse management was no exception. Understanding best practices and implementing workflows in all areas of warehouse management became the priority and one major area of focus has been warehouse order picking.
WHAT IS ORDER PICKING?
Order picking is the process of pulling items from your inventory to fulfill an order. It sounds so elementary, the process is oftentimes overlooked. But in actuality, it’s a foundational step in order fulfillment. In fact almost 55% of operational costs within any given distribution center. Not so trivial after all. This is why services like third-party logistics are crucial to streamline the process.
3PLs quickly understood that ineffective order picking could lead to inefficient processes and halted innovation. To avoid these challenges, order picking best practices need to focus on speed, accuracy, and warehouse organization.

AUTOMATION AND WAREHOUSE LOGISTICS
It wasn’t too long ago, warehouses used paper picklists to track order fulfillment. Those days are long gone with new technologies and automated systems that can organize inventory, warehouse location, and even best routes to the location of an item.
Here are a few of our favorite automated programs:
- Pick to light: a type of order-fulfillment technology designed to improve picking accuracy and efficiency, while simultaneously lowering labor costs. Pick to light employs alphanumeric displays and buttons at storage locations, to guide employees in light-aided manual picking, putting away, sorting, and assembly.
- Voice picking: also commonly known as voice-directed warehousing (VDW), pick by voice, and speech-based picking, is a paperless, hands-free, and eyes-free system that employs easy-to-understand voice prompts to direct warehouse operators to pick locations and to instruct them in picking tasks.
- Mobile scanner picking: the newest barcode scanners have cutting-edge features that promote automation throughout the supply chain. Today’s best barcode scanners cut down the possibility of human error, eliminate paper and printing costs, give time-saving information on SKU location, and are hooked up to software that automatically analyzes your inventory.
These technologies have helped supply chains reduce costs, streamline operations, and save valuable time. And thats just the start! For instance, understanding the intricacies of what transloading is can further enhance the efficiency of these systems.
IMPROVE WAREHOUSE PRODUCTIVITY
Implementing automation and technology can vastly improve warehouse order picking efficiency, but there are other ways to also increase warehouse productivity. Capitalizing on technology, innovative methodologies, and update to date processes will all contribute to cost savings and faster, more accurate fulfillment orders. Other ways to improve productivity include:
♦ Prioritize replenishment: popular items move quickly and tracking inventory and availability can reduce fulfillment and picking time. Keep your most popular items readily available, clearly labeled, and easy to locate within your warehouse
♦ Warehouse layout: a warehouse should easily flow from one key area to the next. Most orders follow a fairly standard warehouse process starting with receiving, storage, fulfillment, picking orders, packing, and shipping. Reduce order fulfillment time by having your warehouse mimic this process, eliminating staff and automation from having to backtrack throughout the facility.
♦ Goods to Person technology: technology (such as AS/RS, carousels, and flow racking) reduces the need for human involvement in the picking process. It also cuts down overall travel time, human fatigue, and the number of steps required to pick orders, thus speeding up the order fulfillment process. Most importantly, it removes the need for personal interaction during picking activities, a significant benefit as warehouses are implementing social distancing measures to keep employees safe in the midst of the COVID-19 pandemic.
♦ Implement an inventory handling process: implement an inventory handling process that best fits your business practices. A common practice is FIFO, or “first in, first out”, but it is not necessarily for everyone. Most often, FIFO is beneficial for companies looking to rotate their inventory so the goods stored don’t expire or reach the end of life before they are used. However, LIFO, “last in, first out”, works well in certain environments.
TECHNOLOGY + PRODUCTIVITY = OPTIMAL FULFILLMENT

About the Author
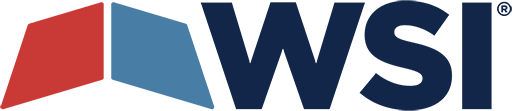
WSI Team
WSI is one of the largest privately held 3rd party logistics companies in the U.S. and spans a nationwide distribution network with global logistics reach.