What Does ‘In Fulfillment’ Mean?
THE ORDER FULFILLMENT PROCESS
When a customer decides to place an order and make the payment, the order fulfillment process begins. The order will go through a typical five-part process.
The first step involves receiving the order. Companies have various ways to take orders. They may offer one or more sales order processes, such as over the phone, electronic data exchange (EDI), in person, online through a company-operated web page, or over a marketplace platform.
Once the order is received, it is processed and the data enters the network system. During this stage, a sales rep may determine the best way to complete the order by selecting the fulfillment distribution center or warehouse that is located closest to the customer.
Alternatively, a company may have this part of the process automated to ensure the right data is pulled from the order to complete the rest of the fulfillment process. The customer is usually sent an update regarding the status of the order, such as ‘order processing’, ‘in fulfillment’ or ‘shipping’.
The next two steps in the order fulfillment process are picking inventory and preparing the products for shipment. These processes are usually accomplished by an order fulfillment associate who locates the products on the shelves, ensures all items are gathered for the order, and packs the products for shipping. He or she might also send updated inventory data through a warehouse management system so that sales associates know how much inventory is still available for purchase.
Once the packing is complete, the shipping process begins. This shipping task may mean the order is sent directly to the customer or to a distribution center for further logistical steps.
Typically, after the product is shipped and delivered, the order process ends. On some occasions, however, the customer may be dissatisfied with the order. This dissatisfaction may result in a return. A good company will follow its return policies when engaging with the customer and offer either a replacement product or refund.
‘IN FULFILLMENT’ STATUS
When a customer reviews an order through an online portal, he or she may see different status updates. These updates may say ‘order processing’, ‘awaiting fulfillment’, ‘in fulfillment’ or ‘awaiting dispatch’, among other language. The fulfillment status updates relate to the progress that the order is taking through the company.
ORDER PROCESSING
Order processing simply means that the company has successfully received the customer’s order and is inputting the data information into its systems. A customer has a short window of time to make any changes at this point or to cancel the order before it moves into the next fulfillment stage.
AWAITING FULFILLMENT
A customer may ask, “What does ‘awaiting fulfillment’ mean, and how does it differ from order processing?” When an order is awaiting fulfillment, it means that the order processing has been completed and sent to the warehouse. However, the fulfillment associate has yet to begin picking and packing the order.
IN FULFILLMENT
What does ‘in fulfillment’ mean? This fulfillment status means the fulfillment associate is now getting the products from shelves to complete the order. She or he is also packing the products for shipment. Typically, a company will not accept any order changes at this point in the process.
AWAITING DISPATCH
Awaiting dispatch means that the products have been picked and packed. The order is now waiting to be picked up and delivered via the chosen delivery method, whether it involves internal delivery drivers, a 3PL or a delivery company.
When it comes to a fulfillment definition, it varies based on where the order is during the fulfillment process. ‘In fulfillment’ simply means the order is in the picking and packing stage.
BENEFITS OF ORDER FULFILLMENT
Having a versatile and robust order fulfillment process as part of your warehouse services allows you to increase customer satisfaction and build your customer base. With an efficient fulfillment process, order turnover rates can move at an appropriate pace and inventory can stay at the right level — without overstocking on products or running out of items.
In addition, using status updates can also help avoid confusion for customers who wish to change their orders or adjust quantities at the last minute. A status update gives them the right amount of time to make changes without causing disruptions or bottlenecks in the rest of your supply chain.
DISCOVER THE WSI DIFFERENCE
The order fulfillment process involves many phases that must work in sync with each other. When warehouse processes are optimized, a company can ensure customer satisfaction while successfully managing inventory levels.
WSI is a 3PL that offers warehouse and distribution services to ensure that orders get processed and sent to destinations. Contact us today to learn more about our processes.
About the Author
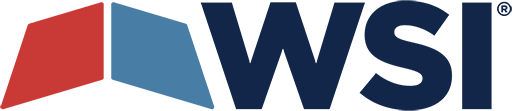
WSI Team
WSI is one of the largest privately held 3rd party logistics companies in the U.S. and spans a nationwide distribution network with global logistics reach.