A Chemical Logistics Partner Matters When It Comes to Regulations
Storage and handling of sensitive materials has its complexities. Regulations from local through federal levels ensure safe chemical management, protecting workers, businesses, and local communities. Working side by side with a chemical logistics partner in this specialized discipline is an invaluable tactical investment.
How to Understand Chemical Regulations
Manufacturers producing raw materials for basic chemicals have a lot to contend with from health, safety, and regulatory compliance standards, invariably passing some of the same responsibilities onto the storage facilities and transportation companies handling those products.
Federal agencies involved in regulating chemical materials handling include OSHA, EPA, PHMSA, and DOT, while state agencies regulate how hazardous materials are disposed. With multiple rules to comply with, it’s hard to know what to follow and when.
As a good rule of thumb, businesses working with chemicals can distinguish between federal and state guidelines as:
- Federal agencies have enforcement authority, above state agencies
- Federal chemical transportation regulations cannot be superseded by state agencies, but they can decline enforcing them
Compliance with both federal and state regulations ensure safe operations for all.
Guidelines to Safe Chemical Storage
Global supply chains rely on chemical compounds for industrial use, like plastics, oil and gas, energy production, and construction, impacting pharmaceuticals, household goods, and more. Whether the hazardous materials are in a pre-production state or ready-to-market, their toxic and reactive qualities present risks during storage and transit.
OSHA and other agencies work together under a large umbrella of safety protocols that cut through language and trade barriers. By using signs and labels, there is a worldwide understanding of how to approach the handling of chemicals in a variety of environments. As hazardous substances move from location to location, workers are required to follow the same guidelines ensuring the health and safety of those on the premises and in surrounding areas.
Chemical Classifications, Labels, And Safety Data Sheets
In 1983, OSHA created the Hazard Communication Standard (HCS) requiring manufacturers to classify hazardous materials and provide SDS. These sheets relay health hazards, emergency response instructions, and ensure access to critical safety data. HCS serves as a collective hub for employers and employees to learn and train for the proper handling and transportation of chemical materials and enacting appropriate emergency responses if disaster strikes.Â
Picture Perfect
Before a chemical transport provider encounters a hazardous materials load, the product manufacturers and importers evaluate the contents and apply labels for each hazard class and category, and provide safety data sheets for each end customer so there is no mistaking what’s inside and how to manage it.
Each label includes a pictogram, an illustrative sign representing a specific type of hazard. There are nine in total, each framed in a red diamond, with a black hazard symbol on a white background in its center.
Hazmat labels also show a signal word, hazard and precautionary statements, a product identifier, and supplier identification. Once a chemical logistics provider receives a load with hazardous material, the manufacturer’s labeling, branding, and notifications must remain until material residue is removed from the container and cleared of lingering vapors.
Look to safety data sheets for:
- Description of material’s health hazards
- Recommended safe work practices
- Verification by chemical manufacturers for their product purchasers
- Easy access of hazardous chemicals information from employer-to-employee
Having the proper information noted on hazardous material bins, containers and packages is the first step in a long journey to chemical storage, transportation and delivery.

Chemical Transportation Across the Nation
Not all warehousing facilities and transloading, docking, and shipping locations are versed in chemical logistics, which adds more risk to potentially dangerous scenarios. Like other products moved from carrier to distributor to end-user, finding the right 3PL provider can save costs, time, and help mitigate risks.
Before selecting a chemical logistics partner, the following questions can help separate the winners:
- How many stops are required when transporting hazardous materials?
- What is the best form of transportation (rail vs. truck)?
- Is there capacity for chemical storage? =
- Does the chemical 3PL provider have hazmat trained staff available?
In the best of circumstances, people and process work interchangeably to ensure health, safety, and efficiency in dealing with chemical substances. Proper training reduces risk and ensures compliance with DOT regulations for chemical transportation.
Skilled Hazardous Chemical Workers Save Lives
Warehouses and loading docks operate under a duty of care for the safety of their workers, contractors, and third-party vendors who come on site. Chemical storage and the movement of those products adds more layers to the duty of care, magnifying the importance of vigilant regulatory practices.
For companies working in the transportation of hazardous materials, employees are required to complete and maintain HazMat training. The learnings cover general awareness of Hazardous Materials Regulations and a solid understanding of HRC (Highly Reactive Chemical) safety standards, how to avoid accidents, and what to do after exposure. And with security threats running high across supply chains, HazMat training addresses security risks and how best to respond to them. Different modes of transportation carry varied regulations and the training covers rail, public highway transit, and others.
Still not sure if a chemical logistics partner needs the HazMat certification?
Direct and Indirect HazMat Needs
HazMat training is required for employees who assist with:
- loading, unloading, or handling
- preparation for transportation
- vehicle operator for transport
- responsibilities involved in the safety of their transportation
- reconditioning, repairing, modifying, marking, or otherwise representing containers, drums, or packaging for use during their transport
Companies hauling chemical materials carry risks. Even with skilled workers and up to date training in place, situations can arise putting precautionary and mandatory safety measures into question.
Protecting Against the Unthinkable
In February 2023, a Norfolk Southern 150-car train hauling vinyl chloride, butyl acrylate, isobutylene, ethylene glycol, and ethylhexyl acrylate derailed in Palestine, Ohio. There were concerns about levels of contamination in the air, water and soil affecting nearby neighborhoods.
A decision had to be made to lessen the risk of a polymerization reaction explosion in one tank car; resulting in the toxic chemical’s release into a trench, burning for 72 hours. While the EPA conducted thorough investigations and tested for health hazards, other environmental experts questioned whether enough was being done to assess the short- and long-term damage to the community.
After the derailment was deemed 100% preventable, and the companies directly and indirectly involved in the transport of the chemicals went through rigorous inquiries, having accurate and verifiable data to identify the chemicals on board was instrumental in providing the necessary response.
The Cost of Sub-Standard Chemical Storage
What keeps logistics professionals up at night are the risks associated with chemical storage and the transit of hazardous materials. The primary danger is from chemical reactivity, where the materials from one spur a strong reaction in others, causing explosions, fires, and the release of toxic gases.
And during transit from dock to warehouse and freight trucks to delivery, logistics workers and chemical operators know the increased risks that come with the territory.
Three hazardous materials posing the most risk in transit is:
- Flammable gases and liquids
- Explosives
- Corrosives
The added vulnerabilities presented when shipping chemicals across the country put more stress on supply chains carrying this type of cargo.
To ensure customers, communities, and strategic partners are kept safe while hazardous materials are stored or in transit, an expert chemical logistics provider can assist in planning and protecting products, people and process, providing peace of mind.

About the Author
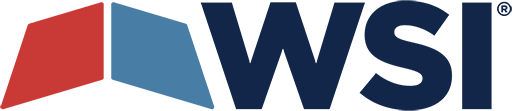
WSI Team
WSI is one of the largest privately held 3rd party logistics companies in the U.S. and spans a nationwide distribution network with global logistics reach.