Warehouse
Storage Guide
Optimizing Your Space
for Efficiency and Safety
Efficient warehouse storage is the backbone of a streamlined supply chain, ensuring products are stored safely, accessed easily, and moved efficiently. However, what “efficient warehouse storage” actually means can vary for those who attempt to achieve it because warehouse storage encompasses a wide variety of storage methods and practices.
Selecting the ideal warehouse storage system takes expertise and effort, but the payoff can be remarkable. At WSI, we understand these complexities from nearly six decades spent working closely with business owners, logistics professionals, and warehouse managers. We offer expert guidance in warehousing services alongside innovative storage solutions tailored to meet the unique needs of businesses across various industries.
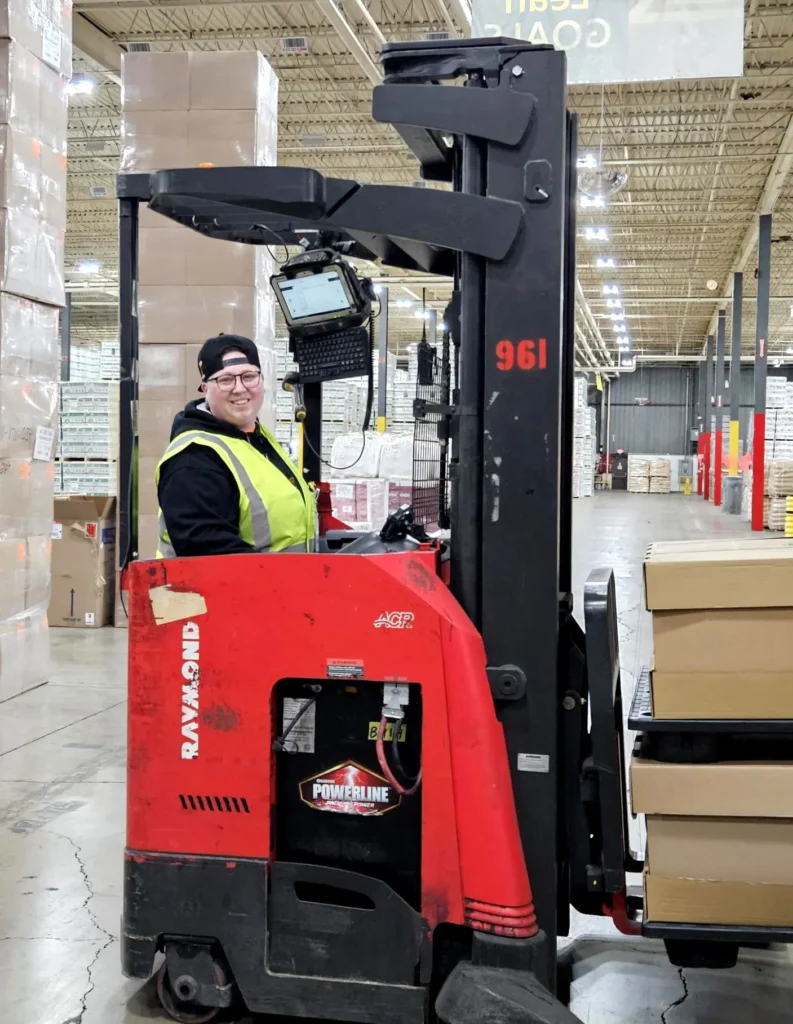
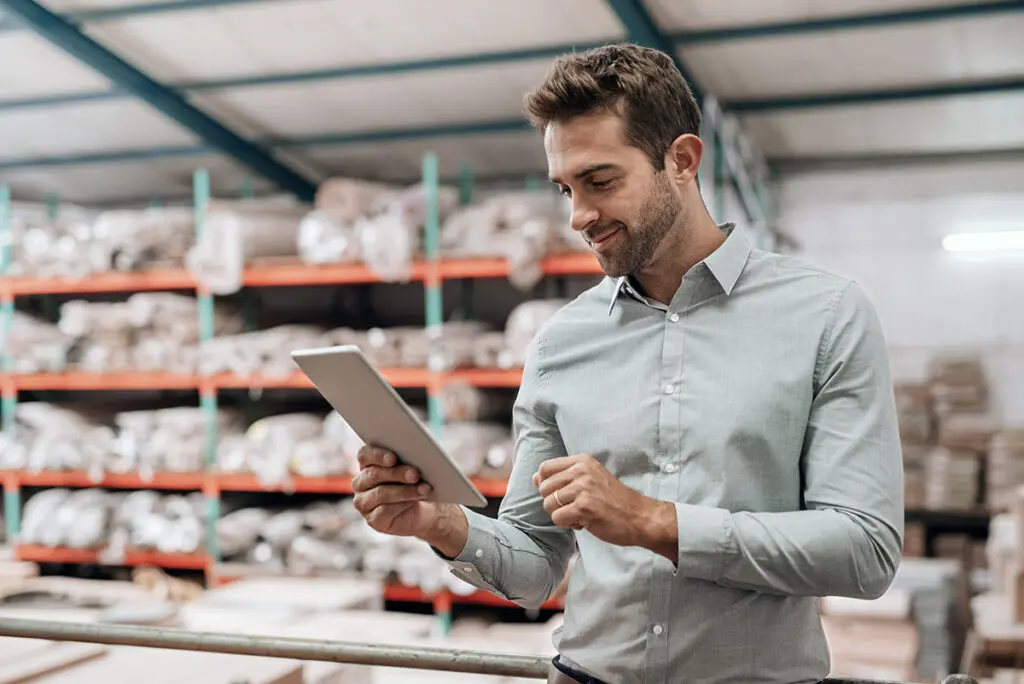
Understanding Your
Storage Needs
Before diving into all of the warehouse storage options, it’s important to first assess your storage needs comprehensively. Consider the types of products you’re storing, focusing on their size, weight, and quantity. It’s also essential to evaluate the frequency of access and inventory turnover. How often do you need to access which products?
These factors can influence your choice of storage solutions. By aligning your storage strategy with the below considerations, you can ensure a seamless product flow and optimize your warehouse’s overall functionality.
Bulk Storage Solutions
Bulk storage represents a fundamental solution for accommodating large volumes of inventory. It’s especially suited for storing large items like equipment, furniture, and oversized rolls of paper.
However, bulk storage isn’t a one-size-fits-all solution. Items that cannot be stacked, such as jewelry or perishable foods, and products requiring individual picking or rapid warehouse movement, may not be ideal for bulk storage.
Sometimes, the most efficient use of bulk storage involves using it in concert with another storage solution, like this recent case study. By partnering with WSI, a high-end furniture and home decor brand was able to leverage both bulk and rack storage, optimizing their warehousing costs.
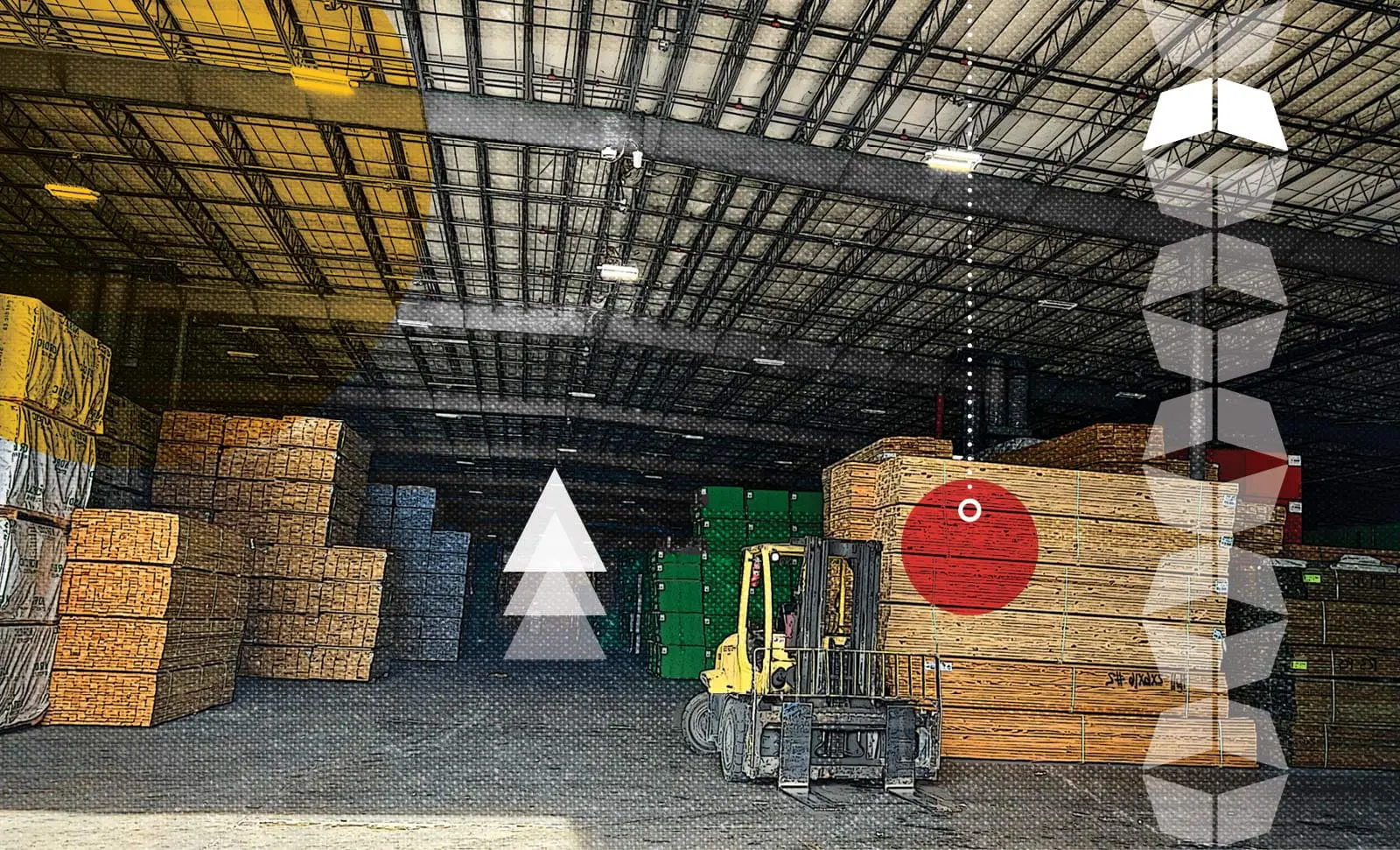
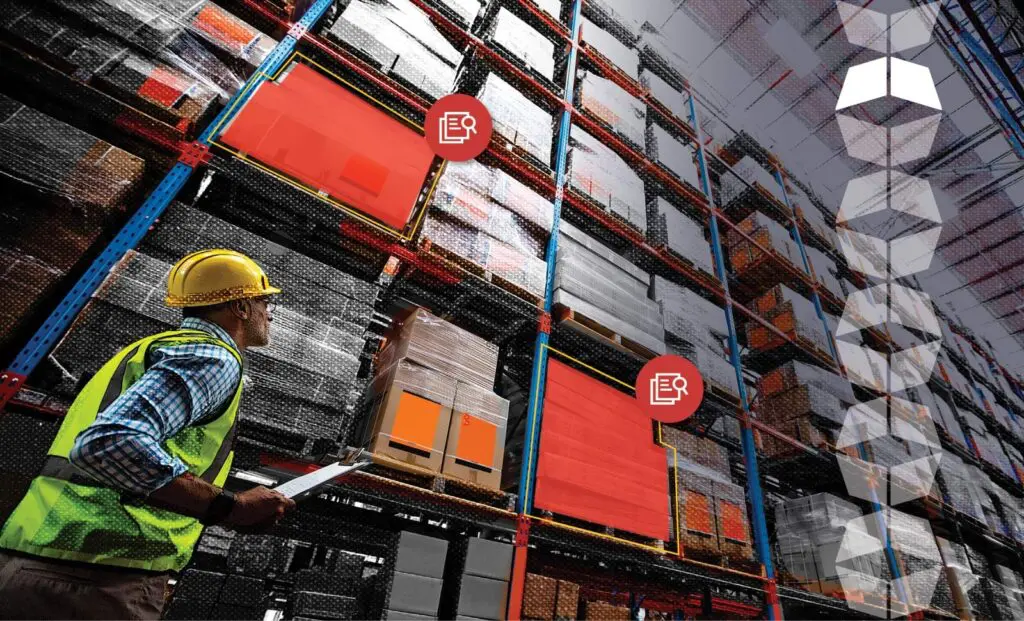
Pallet Racks &
Their Versatility
Pallet racks are a staple in warehouse storage, offering an easy path to correct product flow in a warehouse. These storage systems are especially invaluable for items that require elevation from the floor and cannot be stacked to great heights. Pallet racks are also highly versatile, catering to a wide range of storage needs, from food-grade items to eCommerce fulfillment products.
However, they come with their own set of limitations, particularly concerning the height and weight of the stored items. WSI leverages pallet rack systems to maximize storage efficiency, drawing on best practices and extensive experience to accommodate diverse storage requirements.
Maximizing Efficiency
with Flow Racks
Bulk storage represents a fundamental solution for accommodating large volumes of inventory. It’s especially suited for storing large items like equipment, furniture, and oversized rolls of paper.
However, bulk storage isn’t a one-size-fits-all solution. Items that cannot be stacked, such as jewelry or perishable foods, and products requiring individual picking or rapid warehouse movement, may not be ideal for bulk storage.
Sometimes, the most efficient use of bulk storage involves using it in concert with another storage solution, like this recent case study. By partnering with WSI, a high-end furniture and home decor brand was able to leverage both bulk and rack storage, optimizing their warehousing costs.

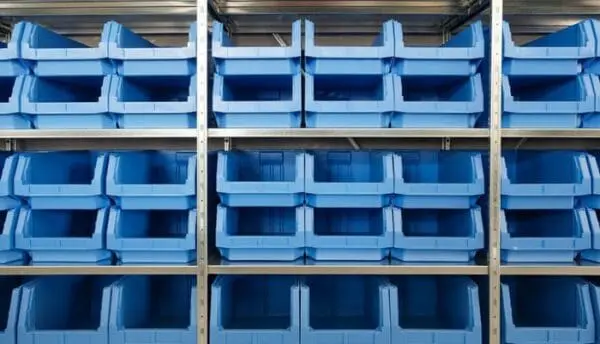
Utilizing Bins for Flexible Storage
With their wide range of sizes and number of flexible configurations, bins are a great option for many products. Whether it’s hardware parts, electronic components, or consumer goods, bins provide a secure and organized storage method. This adaptability makes bins an essential element for many storage solutions, particularly for items that require segregation, easy access, or are too small for pallet racking. Their minimal limitations mean that — if it fits — almost any item can be efficiently stored in a bin.
At WSI, we understand that the effectiveness of bin storage lies in its correct application — matching the right bin size and type to the specific needs of the products being stored. Our expertise in logistics and warehousing solutions allows us to optimize bin storage for maximum efficiency, ensuring that every square inch of warehouse space is utilized effectively, thereby streamlining operations and reducing retrieval times.
Shelving for Small or Fragile Items
Shelving is particularly helpful for the storage of small or fragile items. The strategic use of shelving can significantly enhance the organization, accessibility, and protection of your inventory. Ideal for products such as watches, makeup, and small electronics, shelving ensures that delicate items are stored securely and are easily accessible.
To maximize the benefits of shelving, organizing shelves to enhance productivity and space utilization is crucial. Effective shelving organization often requires categorizing items by type or frequency of use, employing clear labeling for easy identification, and adjusting shelf heights to accommodate different product sizes. Such practices not only improve the efficiency of picking and packing processes but also contribute to a safer and more orderly warehouse environment.
WSI’s shelving solutions are designed with the needs of modern warehouses in mind. By focusing on durability, adaptability, and ease of use, our shelving systems can significantly impact operations. Through careful planning and implementation, WSI ensures that shelving not only meets the immediate storage needs of small or fragile items but also supports the broader objectives of inventory management and supply chain optimization.
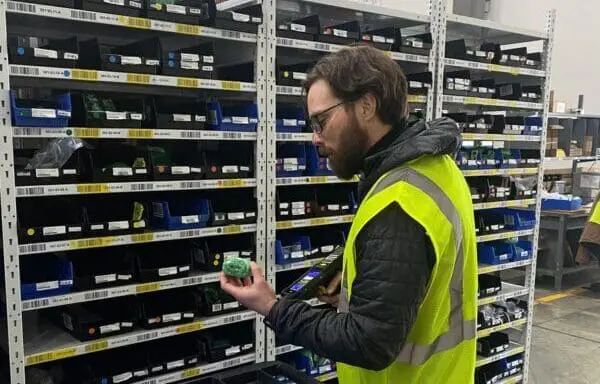
Specialized Chemical Storage
Navigating the complexities of chemical storage presents a unique set of challenges, requiring a nuanced understanding of the diverse properties and potential hazards associated with different chemicals. The essence of specialized chemical storage lies in its ability to address these challenges head-on, ensuring safety, compliance, and efficiency.
The storage requirements for chemicals vary significantly based on their properties. Flammable liquids, corrosive substances, and reactive chemicals each demand distinct storage solutions to mitigate risks and protect both the products and the personnel handling them. For instance, flammable chemicals require storage solutions that minimize the risk of ignition, while corrosive materials require containers and shelving resistant to chemical damage.
WSI stands at the forefront of specialized chemical storage because we understand Reliability is Everything® . Our expertise extends to managing the intricate requirements of chemical logistics, ensuring that every chemical, whether it’s a raw material or a finished product, is stored under optimal conditions. Our facilities are equipped to accommodate the diverse needs of chemical storage, from segregating incompatible substances to implementing stringent safety protocols. With WSI, clients can trust our commitment to maintaining the highest standards of safety and compliance in chemical storage.
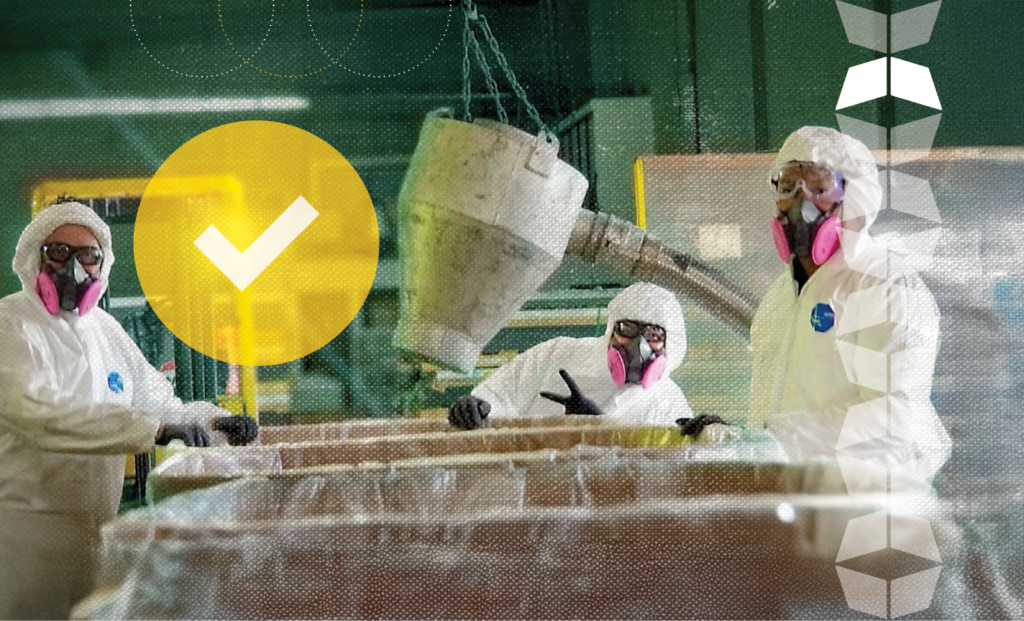
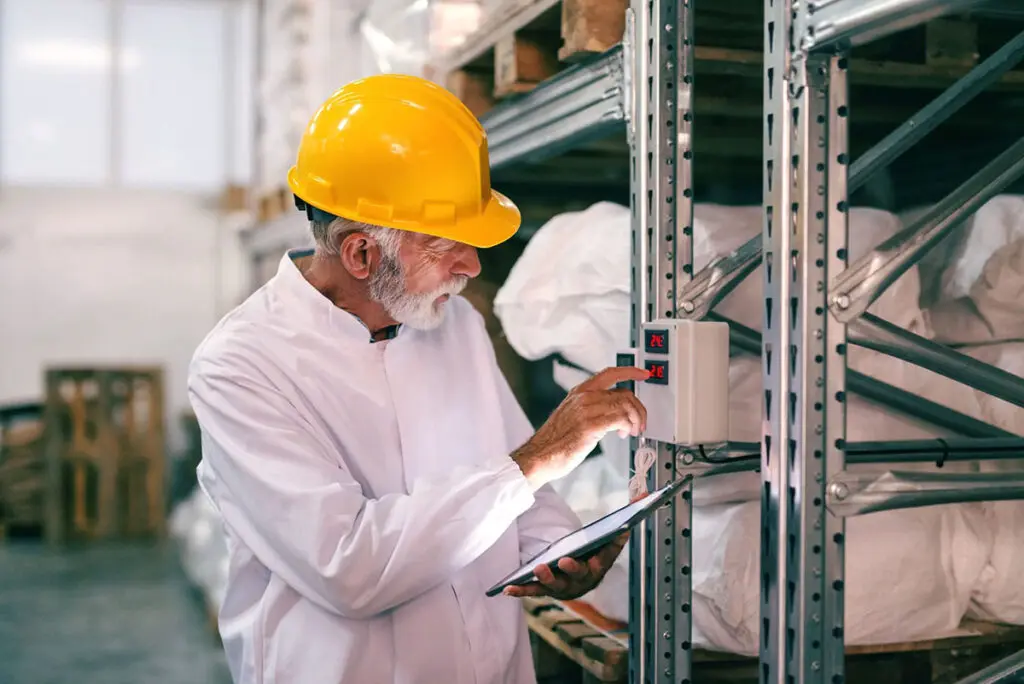
Temperature-Controlled Storage
The importance of temperature control in chemical storage cannot be overstated. Many chemicals are sensitive to temperature fluctuations, which can alter their composition, reduce their effectiveness, or even render them hazardous. Temperature-controlled storage is thus a critical component of specialized storage solutions, designed to maintain stable environmental conditions tailored to the needs of the products stored.
WSI offers advanced temperature-controlled storage solutions for chemicals, leveraging state-of-the-art technology to ensure precise temperature management. Our chemical storage facilities are equipped with climate control systems that monitor and adjust temperatures to meet the exact requirements of each product. Our commitment to utilizing technology in temperature management underscores our dedication to excellence in logistics and warehousing, ensuring that every product entrusted to us is stored under the ideal conditions for safety, quality, and reliability.
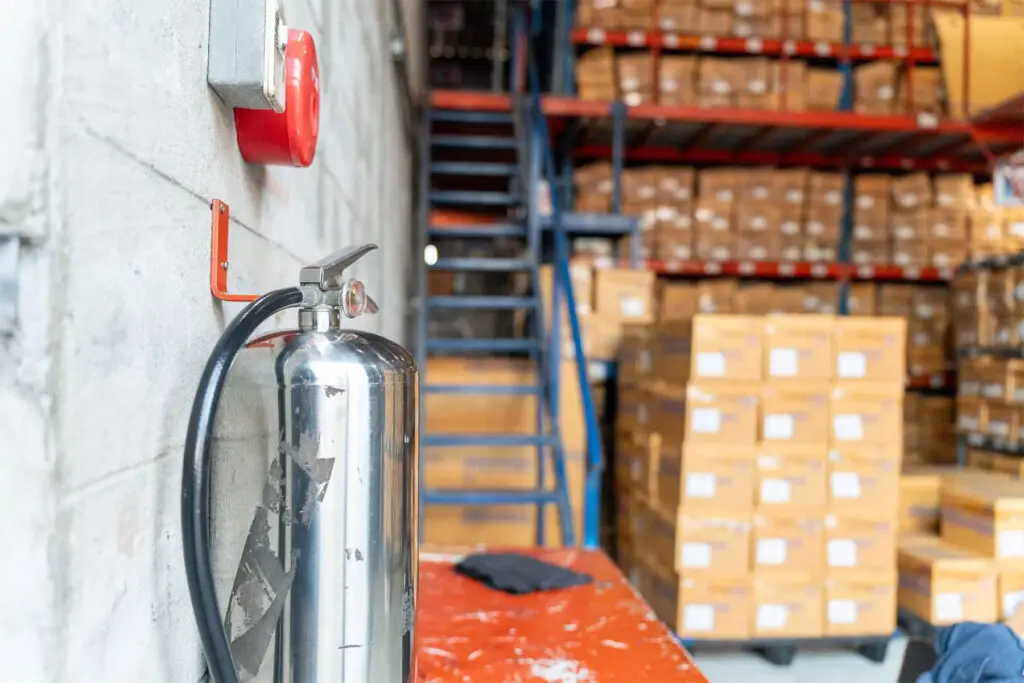
Flame Resistant Rooms and Safety Measures
Storing materials that are flammable or combustible requires an environment designed to significantly reduce the risk of fire, thereby protecting not only the inventory but also the safety of personnel and the facility itself. This specialized storage solution is essential for materials that, if ignited, could lead to catastrophic outcomes. Flame-resistant rooms and safety measures aren’t just a regulatory compliance concern, but a fundamental element of risk management and operational integrity.
WSI takes a proactive approach to ensure safety and compliance with flame-resistant solutions. Our commitment to safeguarding both our clients’ goods and our team members is reflected in the meticulous design and operation of our flame-resistant storage areas. These specialized rooms are constructed using materials that can withstand high temperatures and are designed to contain fires, preventing them from spreading to the warehouse. Additionally, these areas are equipped with advanced fire suppression systems that are automatically activated in the event of a fire.
Beyond the physical infrastructure, WSI implements stringent safety protocols and training programs for our staff, ensuring that everyone is well-versed in handling hazardous materials and responding effectively to emergencies. Regular audits and inspections are conducted to ensure that all flame-resistant rooms and safety measures meet or exceed industry standards and regulations.
Advanced Storage Technologies and WSI’s Investments
Warehouse storage and logistics are continually transformed by the advent of advanced warehouse technology. These innovations not only enhance operational efficiency but also significantly improve accuracy, safety, and customer satisfaction. From automated storage and retrieval systems (AS/RS) to sophisticated warehouse management software (WMS), technology plays a pivotal role in driving new efficiencies and optimizing warehouse operations and supply chain management.
At WSI, we recognize the critical impact of technological advancements and continue to make strategic investments in state-of-the-art warehousing technologies. As highlighted in our exploration of the need for advanced technology in eCommerce, WSI leverages cutting-edge solutions to meet the dynamic demands of the eCommerce sector and beyond. These technologies enable us to offer unparalleled efficiency, accuracy, and speed in handling our clients’ storage and logistics needs, ensuring that we stay at the forefront of industry innovations.
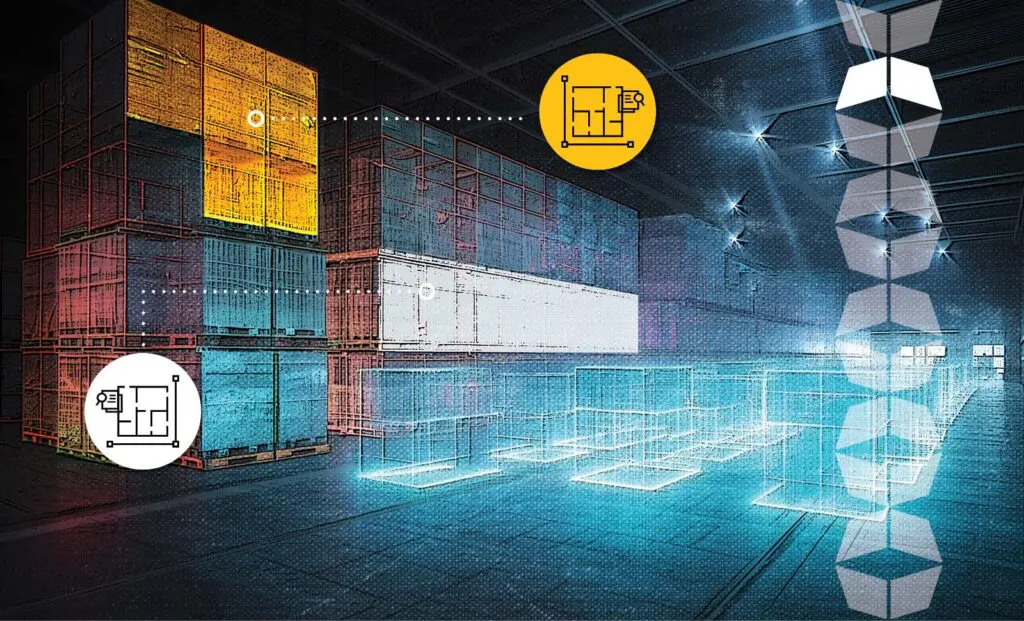
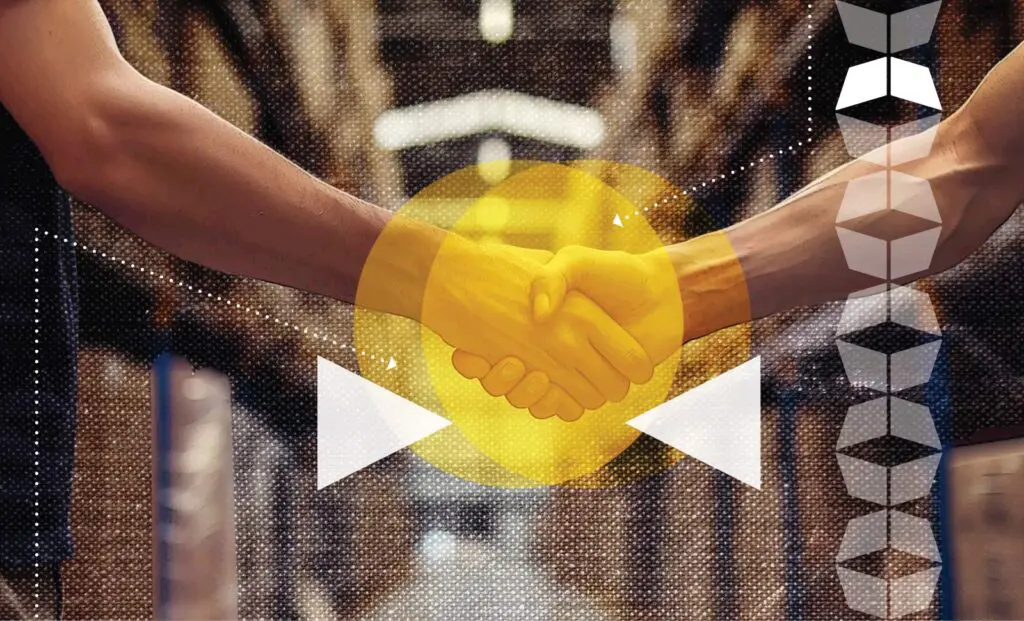
Crafting an Optimal Supply Chain Strategy with WSI
At WSI, our Condition, Count & Time® promise is at the heart of our approach to storage and logistics, ensuring that every item is stored and handled with the utmost care, accuracy, and efficiency. By prioritizing the condition of goods, accurate inventory counts, and timely processing, we help our clients streamline their supply chains, reduce costs, and improve customer satisfaction.
Customizing storage solutions based on individual business needs is a cornerstone of our strategy. We understand that each business has unique requirements, and a one-size-fits-all approach is not sufficient. By working closely with our clients, we develop tailored solutions that address their specific challenges and objectives, leveraging our expertise and technology to enhance their supply chain efficiency.
Our success in implementing effective supply chain strategies is evident across our customer success stories. In one instance, a comprehensive supply chain analysis revealed efficiency gaps in a client’s warehousing operations, leading to strategic adjustments that significantly improved their operations. Another case study showcases how a 3PL partnership with WSI increased operational flexibility and reduced costs for a client, demonstrating our ability to adapt and deliver solutions that meet the evolving needs of businesses. These examples underscore WSI’s expertise in crafting and executing supply chain strategies that drive success and growth for our clients.
WSI’s Core Values &
Their Role in Storage Solutions
At WSI, our core values of Safety, Accountability, Respect, and Innovation are the foundation for everything we do. These values guide every decision we make, ensuring that we not only meet but exceed the expectations of our clients and stakeholders.
Safety
Safety is paramount in all our operations. We understand the critical importance of maintaining a safe environment for our employees, clients, and their goods. This commitment to safety is evident in our rigorous protocols and state-of-the-art storage facilities, designed to minimize risks and protect assets at all costs.
Accountability
Accountability is at the heart of our promise to clients. We ensure accuracy, reliability, and transparency in every aspect of our service. This sense of accountability fosters trust and confidence among our clients, knowing that their interests are always our top priority.
Respect
Respect underpins our interactions with customers and employees. We value every relationship and strive to understand and meet the unique needs of each client. This respect is reflected in our personalized approach to storage solutions, where we listen to and address the specific challenges and objectives of our partners.
Innovation
Innovation drives our pursuit of excellence. We continuously seek out and implement the latest technologies and best practices in warehousing and logistics. This innovative spirit allows us to offer advanced storage solutions that optimize efficiency, reduce costs, and enhance the overall supply chain.
Warehouse Storage Solutions: Frequently Asked Questions
Warehouse Storage Guide: Conclusion
Selecting the right storage solutions is crucial for the success of any business that needs to store and distribute goods. The right partner can help navigate the complexities of warehousing, ensuring that your products are stored efficiently, safely, and in a manner that supports your business goals.
WSI stands ready to offer expert guidance and customized warehousing strategies that align with your specific needs. If you’re looking for assistance in addressing your storage and warehouse strategy, reach out to WSI today for a consultation.
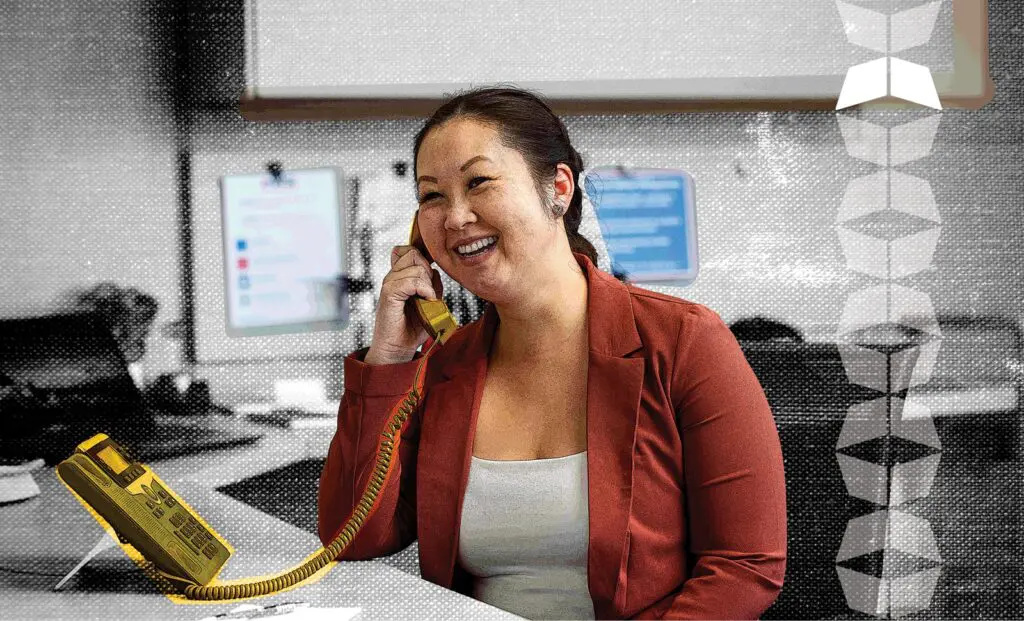
Contact Warehouse Specialists
Whenever you’re ready, give us a call. We’ll have a few questions for you that will help us best figure out how to reliably store and ship your wares. From there, you can sit back, leave the logistics to us, and get back to your business.