10 Things to Look For in a Chemical Logistics Provider
Choosing a 3PL to handle hazardous materials isn’t just a logistics decision, it’s a safety decision. Whether you’re storing chemicals, shipping them across regions, or managing compliance audits, your provider has to be more than just capable. They need to be experienced, detail-obsessed, and fully prepared for what’s at stake.
Below are 10 things to look for in a chemical logistics provider and the questions you should ask to make sure they’re up to the task.
The 10 Must-Haves
Whether you’re reevaluating your current partner or exploring options for the first time, these ten traits will help you select a qualified chemical logistics provider. These must-haves will enable you to find a 3PL equipped to handle the complexity of chemical warehousing and transportation with the safety, compliance, and precision your business depends on.
1. Proven Experience Handling Hazardous Materials
It can be tempting to select an economical provider. However, the risks outweigh any savings you might experience by partnering with a lower-cost 3PL to store and move your chemicals. Not all 3PLs are equipped or qualified to handle hazmat or regulated substances. Your chosen partner must demonstrate a clear track record of managing within the specific regulatory frameworks and have established practices and procedures.
Look for specific examples of experience with your type of product or industry. Don’t assume a 3PL that handles one type of chemical is necessarily qualified or knowledgeable about handling another type. Firsthand experience with your product category or industry ensures fewer missteps and faster onboarding.
2. Regulatory Compliance and Audit Readiness
A qualified chemical 3PL must comply with federal, state, and local agency regulations. These include EPA environmental standards, OSHA workplace safety rules, DOT hazmat transportation laws, and DHS security requirements. Compliance isn’t a one-time event; it’s an ongoing commitment that requires training, documentation, and rigorous operational controls.
Ask potential partners about their most recent audit results, how they prepare for inspections, and what systems they use to track regulatory updates. A reliable partner should be able to provide documentation, demonstrate transparent reporting practices, and demonstrate readiness for unannounced audits.
3. HAZWOPER-Certified and Trained Staff
Handling hazardous materials safely requires specialized training. Any 3PL working with chemicals should have HAZWOPER-certified staff who are regularly trained in the best practices for hazardous material handling. This certification ensures that staff are trained to safely handle hazardous materials and respond to chemical emergencies in compliance with OSHA standards.
Staff should be trained in PPE use, SDS access, spill response, and emergency protocols because well-prepared teams prevent incidents before they happen. Well-trained staff reduce risks and create consistently safe, compliant operations.
4. Facility Design and Safety Standards
Hazardous materials warehousing requires facilities specifically designed for chemical storage. Key features to look for include secondary containment systems to prevent leaks from spreading, fire suppression systems suited for chemical fires, proper ventilation, and temperature and humidity controls to protect product integrity.
Additionally, ask how the facility separates incompatible materials, such as acids and bases or oxidizers and flammables. Safe chemical storage depends on proactive design to prevent incidents before they happen while meeting regulations.
5. Inventory Accuracy and Lot/Batch Control
Regulated chemical inventory must be traceable and accurate. Every unit must be traceable by lot or batch number, with clear records of where it’s been, how long it’s been there, and when it’s scheduled to move. Gaps in visibility can create compliance risks, product integrity issues, and costly delays. A strong chemical 3PL partner maintains detailed, error-free records of every unit’s movement, storage conditions, and status.
The right chemical logistics partner should have systems to support FIFO (First In, First Out), FEFO (First Expired, First Out), and custom inventory logic tailored to your product-specific needs. This ensures proper stock rotation, reduces waste, and helps maintain product integrity from receipt to outbound shipment.

6. Integrated Technology and Visibility Tools
Chemical logistics requires more than manual tracking and spreadsheets. A good provider offers real-time inventory tracking, a robust warehouse management system (WMS), and secure data sharing. This allows you to confidently monitor stock levels, order status, and inventory movement.
Confirm compatibility with EDI, SAP, and other enterprise platforms, and ask whether they offer customer portals for on-demand data access. Seamless system integration reduces errors, improves responsiveness, and keeps your supply chain connected from end to end.
7. Proper Labeling, SDS Access, and Documentation Handling
Accurate labeling and documentation are essential in chemical logistics. A reliable 3PL should meet current standards for hazard labels, placards, and SDS (Safety Data Sheet) access, ensuring all materials are correctly marked, then stored and transported with the correct paperwork.
Labeling errors can lead to shipment rejections, fines, or serious regulatory consequences. Choose a partner who treats documentation with the same precision as physical handling and has established processes to double-check accuracy at every stage.
8. Secure, Compliant Transportation Services
A chemical 3PL should offer transportation capabilities designed for hazardous materials. For instance, can they support drayage, LTL/FTL, intermodal, or rail for chemical shipments?
It’s also important to confirm who potential logistics partners work with. Ask whether they work with hazmat-certified carriers and drivers who are properly trained and equipped to meet DOT requirements for chemical transport. Secure, compliant hazmat shipments must arrive safely, legally, and without disruption.
9. Responsive Communication and Single Point of Contact
Hazmat logistics require effective communication. Look for a provider who offers clear escalation paths, keeps you informed with timely updates, and staffs a customer service team that understands both logistics and regulatory compliance. This ensures that you receive timely answers from someone familiar with your account when an issue arises.
Ask how often they provide reporting and how frequently they meet with clients to review performance. A dedicated point of contact, supported by a knowledgeable team, makes all the difference when every shipment matters.
10. Strong Track Record and Stable Network
Longevity and consistency matter in chemical logistics. Partner with a 3PL with a long history of consistent performance, low incident rates, and established long-term customer relationships. Longevity often signals operational stability and a deep understanding of what it takes to handle hazardous materials safely.
Also, look for a 3PL partner with a strong distribution network. A provider with a national network built for chemical distribution, including warehouses, carriers, and intermodal connections, can offer flexibility as your needs grow. A strong track record backed by a stable network means fewer surprises and a partner you can trust over the long term.
Questions to Ask Your 3PL
Finding the right hazmat logistics partner requires careful due diligence. A qualified 3PL must meet regulatory standards and know how those standards are applied in day-to-day operations. Asking the right questions can help you recognize providers who understand chemical logistics.
Below are a few key questions to ask, along with examples of strong responses that indicate a provider is prepared and capable:
- “When was your last EPA or OSHA audit, and what were the results?”
A strong response might include recent audit dates, no violations, or swift resolution of minor findings, and a proactive approach to ongoing compliance and inspections.
- “How do you handle lot control and expiration tracking?”
Look for clear systems that support FIFO or FEFO logic, accurate batch-level tracking, and audit-ready documentation tied to each lot number.
- “Do your warehouse teams receive ongoing hazmat training?”
An ideal answer includes HAZWOPER certification, regular refresher courses, training tied to job roles, and documented protocols for emergency response, PPE use, and SDS compliance.
Choosing the Right Chemical Logistics Provider Matters
Chemical logistics require more than general warehousing. Hazardous materials are more sensitive, the regulations are more demanding, and the consequences of errors are more severe. The stakes are higher, and the margin for error is smaller. This is why choosing the right 3PL matters in the chemical space.
Use this list of traits as a guide when evaluating a potential chemical logistics provider. Asking the right questions can help you avoid costly mistakes and protect your team, product, and brand reputation.

About the Author
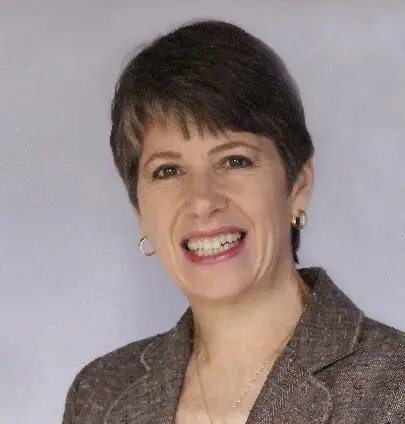
Margot Howard
Margot Howard is a Freelance content marketing writer and strategist with 10+ years of experience. Margot worked in corporate sales for many years before transitioning to content marketing. She writes for B2B SaaS, software, and service companies, especially those in shipping and logistics, Sales Tech, and MarTech.