A Warehouse Layout That Improves Efficiency and Cuts CostsĀ
Every industry has different fulfillment needs, and how their warehouse is set up goes a long way in either hindering or optimizing operational performance.
Take the food and beverage industry, for example. New products arrive frequently, but without a proper first-in, first-out (FIFO) system, older inventory can get pushed to the back, leading to spoilage, increased labor, and lost revenue. If cold storage areas arenāt positioned near shipping and receiving zones, temperature-sensitive items may spend too much time outside their required environment, further increasing the risk of waste, recalls, and lost revenue.
And itās not just this industry. Warehouse layout plays a critical role across the board. Product size, shape, and weight influence storage configurations. High inventory volumes require space for bulk storage. Seasonal surges may call for flexible or temporary layout adjustments.
Thatās why businesses should look for fulfillment partners with expertise in warehouse design and who can adapt to specific industry needs while prioritizing safety, efficiency, and scalability.
Core principles of an efficient warehouse layout
An efficient, cost-saving warehouse layer features four principles: flow, accessibility, space utilization, and safety. When working with a 3PL partner to optimize layout, these should be top of mind:
Flow
Flow streamlines the movement of goods from receiving to shipping and is central to operational efficiency. The layout flow impacts everything, including picking and packing speed, space optimization, and minimizing wasted movement. This leads to faster order fulfillment and reduced costs while improving productivity, inventory management, and enhancing safety.Ā
Accessibility
Accessibility is designing warehouse layout for improved equipment access and product retrieval while also addressing safety. To improve accessibility, fulfillment teams must reduce travel time with clear pathways and give access to items in a way that makes it easy for employees to locate and retrieve orders.
Space utilization
Space utilization affects flow, accessibility, and safety. In other words, itās a key component in warehouse layout. It should maximize vertical and horizontal space, optimize aisle width, and support efficient inventory management systems. Space utilization is generally comprised of a mix of racking systems, carousels, lifts, mezzanines, zones, dedicated areas, and more.Ā
Safety
Safety is paramount to brand reputation, compliance, partnerships, labor force retention, and preventing operational disruptions. This means keeping aisles clear, reducing congestion, and planning for compliance. While the priority should be protecting workers, safety also minimizes financial loss by maintaining product integrity and boosting productivity.
Each industry will have different flow, accessibility, space utilization, and safety needs that affect their warehouse layout. Here are some examples:
Key warehouse layout factors by industry
Factor | Food & Beverage | Chemicals | Retail / Ecommerce | Paper / Packaging | Industrial Goods |
Product characteristic | Perishable, varied sizes, sensitive to spoilage | Hazardous, flammable, requires containment | High SKU variety, small to medium packages | Large pallets, bulky, stackable | Heavy, oversized, durable |
Inventory volume | High volume with fast turnover | Moderate, requires secure storage | High SKU count, fast-moving inventory | Bulk storage with seasonal spikes | High volume with steady demand |
Order profiles | Frequent small orders, strict FIFO | Bulk or batch shipments | High-frequency picks, multi-line orders | Fewer picks, larger quantities per order | Mixed orders with parts, tools, and large equipment |
Material handling equipment | Pallet jacks, chill zone carts | Specialized hazmat forklifts, spill kits | Pick carts, conveyors, AMRs | Standard forklifts, palletizers | Cranes, heavy-duty forklifts |
Seasonality | Holiday, summer drink surges | Less seasonal, but subject to global disruptions | Peak seasons (Q4, back-to-school, promos) | End-of-year bulk orders | Stable, occasional project-based spikes |
Receiving/ shipping volume | High volume, time-sensitive | Controlled flow, requires documentation | Rapid in/outflow, frequent parcel carriers | Infrequent bulk deliveries | Large batch loads, scheduled shipments |
Temperature control | Critical (cold/frozen zones) | May need temp-controlled or ventilated rooms | Optional (beauty, perishables) | Not needed | Not needed |
Compliance & safety | Food-grade standards, HACCP, lot tracking | OSHA, EPA, Responsible CareĀ® standards | Basic OSHA compliance | Clean, dry conditions | OSHA, weight and height stacking regulations |
Labor & workflow | Fast picking & packing, ergonomic layout essentialĀ | Trained staff, safety protocols critical | High picker density, fast packing stations | Moderate staffing needs | Skilled handling, equipment operation |
Technology & automation | Real-time WMS, batch picking, temp tracking | Inventory controls, digital compliance records | Advanced WMS, real-time inventory, robotic picking | Basic WMS integration | Scanning and tracking for industrial parts |
Key layout types and when to use them
While each business and product will have unique warehouse layout needs that can be optimized with the help of a strategic partner, there are some common layouts used for specific types of fulfillment operations. For instance, a U-shaped layout is often ideal for smaller operations that need order control. An I-shaped layout (also known as a throughput layout) is ideal for high-volume, cross-docking, or direct-to-consumer (DTC) environments. Lastly, an L-shaped layout can support specialized flows and operations with separate inbound and outbound areas.
Despite these norms, choosing the right 3PL provider will give businesses access to experts that can tailor warehouse layouts to their specific needs, boosting productivity, efficiency, and cost-savings.
Functional zones and best practices
When creating an optimized warehouse layout plan, businesses should consider four primary zones. This includes the receiving area and dock placement, staging space, and inspection areas, and the storage area, along with features such as pallet racking, bulk storage, and bin shelving, based on product types.Ā Ā
Two other main areas are the picking area and the packing and shipping area. Retailers should look at batch vs zone picking and how to minimize picker travel time for the picking area. The packing and shipping area needs will cover things like workstation design, conveyor access, and staging lanes.Ā
Each industry has considerations that influence warehouse layout. For example:
- Retail and ecommerce have high SKU counts and frequent picking
- Chemicals require hazmat zones, ventilation, and have segregation requirements
- Paper products need bulk storage and the ability to stack goods
- Food and beverage lean on FIFO methodology, cold storage, and sanitation standards
- Furniture or industrial goods will likely require oversized storage zones and accessibility for special handling equipment
Technologyās role in warehouse layout optimization
Modern fulfillment technology has an enormous influence on how efficient operations are. More logistics providers are investing in integrated tech stacks to automate and cut costs. According to McKinsey & Company, automation in logistics and fulfillment is expected to account for more than a third of capital spending. And the investment in tech and automation can help with warehouse layout optimization as well.
Warehouse management systems (WMS), barcode scanning, and automation influence layout decisions by streamlining inventory tracking, guiding picking paths, and reducing manual errors. The real-time data from these systems supports re-slotting to improve storage efficiency as demand shifts. There are also simulation tools that let operations teams model and forecast layout scenarios before making the physical changes.
Relying on 3PL expertise for optimal warehouse layout
Itās essential to be able to rely on a 3PL partnerās expertise to help improve warehouse layout.
Imagine being able to do something such as reducing labor hours by 30% by redesigning layout to shorten picking paths and consolidate high-velocity SKUs near packing stations. By right-sizing storage zones and reconfiguring layouts based on specific inventory and order profiles, 3PLs help ensure space is used effectively. This could mean creating dedicated areas for seasonal overflow or reorganizing bulk storage to improve accessibility.Ā Ā
The right layout isnāt one-size-fits-all; itās about optimizing your operations. Want to improve your warehouse efficiency and boost cost savings? Talk to a WSI expert today about how an optimized warehouse layout can save you time and money.
About the Author
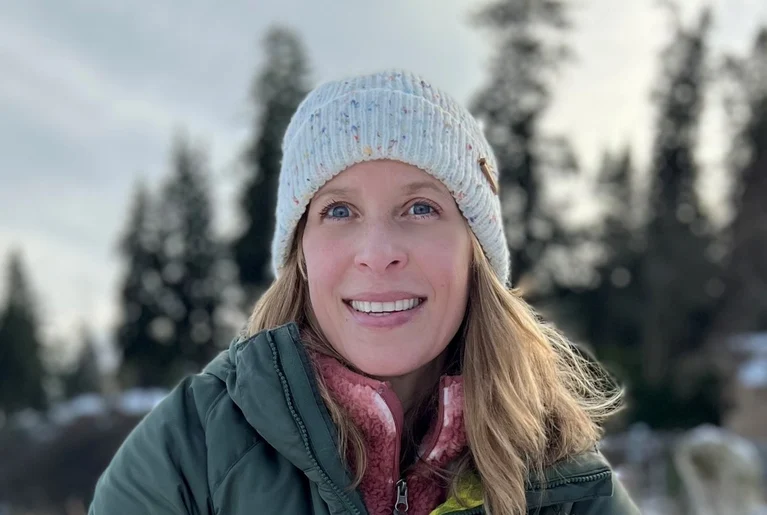
Alyssa Wolfe
Alyssa Wolfe is a content strategist, storyteller, and creative and content lead with over a decade of experience shaping brand narratives across industries including retail, travel, logistics, fintech, SaaS, B2C, and B2B services. She specializes in turning complex ideas into clear, human-centered content that connects, informs, and inspires. With a background in journalism, marketing, and digital strategy, Alyssa brings a sharp editorial eye and a collaborative spirit to every project. Her work spans thought leadership, executive ghostwriting, brand messaging, and educational contentāall grounded in a deep understanding of audience needs and business goals. Alyssa is passionate about the power of language to drive clarity and change, and she believes the best content not only tells a story, but builds trust and sparks action.