Receiving Best Practices That Set the Tone for Fulfillment SuccessÂ
This is an updated post from May 31st, 2023.
“An ounce of prevention is worth a pound of cure.”  Benjamin Franklin purportedly wrote this line to say that it’s typically easier to prevent a problem from occurring versus resolving an issue that’s already begun.
Dentists celebrate this principle daily. One was once overheard saying to a teenager in the chair next to them, “Floss now or a root canal, or maybe death, later – the choice is yours.” Dramatic? Yes. But the point stands.
Franklin was referencing city fire preparedness, the dentist was referencing tooth decay, and believe it or not, the same applies to warehouse receiving and successful fulfillment operations.
Think of receiving as setting the stage for your fulfillment operations. A weak receiving process negatively affects inventory management and accuracy, space usage, and order processing. In high-volume, omnichannel environments, warehouse receiving is the foundation that leads to streamlined shipping. Â
What is the warehouse receiving process?
In warehouse operations, the inventory receiving process is the first step. This is where inbound shipments are inspected, verified, and logged into inventory systems. In a functional environment, warehouse receiving checks shipments against purchase orders, confirms product quality and quantity, labels items, and assigns them to the correct storage locations.
A well-executed warehouse receiving process promotes accurate inventory management by making sure that products are correctly identified and accounted for from the start.
In a problematic fulfillment operation where the warehouse receiving process is poor, issues like the following occur:
- Inventory inaccuracies and stock discrepancies
- Delayed order fulfillment and shipping errors
- Misrouted or mislabeled SKUs
- Increased returns and customer complaints
- Inefficient space utilization and storage confusion
- Disrupted pick and pack workflows
- Higher labor costs due to rework and manual corrections
Why the receiving process matters in warehousing and fulfillment operations
When inbound inventory isn’t received accurately, it creates a ripple effect across the entire fulfillment operation leading to inventory errors, wasted labor, and unhappy customers. Here’s a scenario WSI has worked through in the past with new customers who may not be accustomed to inbound logistics management:
An inbound delivery arrives at a fulfillment center  with many cases. The customer wants inbounds to be received at the “case-level,” which accepts and documents incoming shipments of goods that are packaged and sold in cases.
The “Advanced Shipping Notice” (effectively a packing list) tells the warehouse that each case should contain 20 black socks. As a check, we open one of the cases and determine that in fact there are 16 red socks. Moreover, the customer had thought the item dimensions of the pair of socks were 1” x 1” x 3,” but in reality, the dimensions are 0.5” x 0.5” x 6.” What would have happened if we hadn’t noticed these discrepancies?
Well, first, the inventory takes a hit. Not knowing any better, a Warehouse Management System (WMS) receives the 20 black socks in inventory, meaning the inventory is now wrong. What the system thinks is on-hand is not actually there. Moreover, a contemporary WMS will utilize “directed put-away” to store the product in the optimal location based on SKU velocity and inventory consolidation possibilities to take up less floor space and save the customer money.
If the system has the wrong SKU or count, this practice, intended to drive efficiency and lower costs, becomes a mess: “A” velocity SKUs are put into “C” velocity slots and vice versa; locations are overstuffed with product; etc. Even the best fulfillment software relies on having good data. In other words, garbage in, garbage out.
Second, the picking process is compromised. With the WMS’ inventory off-kilter, Pickers are directed to pick from locations with the wrong product or that are out-of-stock. Now chaos breaks loose; desperately trying to fulfill orders, Pickers start searching everywhere for the product on the order. They take products from other locations vs. the one that was system directed, meaning yet another location’s inventory is undermined without the WMS realizing it. Scanning products (a best practice to ensure order accuracy) becomes less frequent since the WMS may reject the pick from an alternate location. We’re in trouble now.
Finally, the pack-out process begins driving up costs due to inaccurate dimensions. The WMS suggests a box size for Packers based on the product’s cubic footprint. If the dimensions are off, it will cause the system to suggest packaging sizes that are too small (risking damage) or too big (driving up transportation cost). These are both unacceptable outcomes.
The takeaway here is that with the correct warehouse receiving process and best practices in place, downstream issues like stock discrepancies, order delays, and fulfillment errors are avoided, protecting a retail business’s operational efficiency and customer satisfaction.
Warehouse receiving best practices to implement now
Retail businesses that start with a strong inbound process strengthen their operations. This allows for more flexibility, scalability, and resilience. If you’re experiencing any issues tied to warehouse receiving, start with these essential best practices:
1. Standardize procedures and checklists
Nothing beats clear, repeatable workflows for teams to follow. Every shipment should follow the same process and validation steps to minimize mistakes, including:
- Create and enforce receiving checklists across shifts
- Ensure all ASNs (Advance Shipment Notices) are received and validated before physical product arrives
- Use experienced team members to oversee inbound operations for added accuracy
2. Use real-time data capture and sync inventory immediately
Today’s technology lets warehouses capture and sync inventory immediately, eliminating manual errors and keeping accurate inventory levels across systems. Warehouses can do this through barcode scanning or RFID at the case or at each level. However, for mixed SKUs or chronic accuracy issues, receive items at each level. Make sure to measure and weigh new SKUs on arrival to maintain WMS data accuracy.
3. Perform quality control and enforce vendor compliance
A few simple actions allow receiving operations to check the quality control and compliance of vendors. Check for issues early and often by:
- “Sampling” 10–20% of inbound cases to validate SKU and count accuracy
- Verifying that packaging, quantities, and labeling meet your standards
- Logging discrepancies and create a feedback loop to help suppliers improve
4. Design efficient dock and staging areas
Warehouse layout shouldn’t be the only layout you optimize for your fulfillment operations; the physical layout of your warehouse receiving area is critical too. How things are set up influences fast, organized workflows.
Staging zones isolate incoming shipments, while the design layout can help avoid congestion and cross-contamination. When needed, employ FIFO (first in, first out) or cross-docking strategies to improve efficiency.
5. Prioritize clear labeling and systematic putaway
The final step involves fast, accurate placement of inventory into storage. Follow labeling standards to avoid downstream confusion and use a WMS or system-directed putaway to map storage location. Accurate placement means faster picking, reduced search time, and less fulfillment errors. It also maximizes space utilization while keeping operations flowing smoothly.
Partner with a 3PL that prioritizes warehouse receiving excellence
Space optimization, speedy order picking and shipping, and smooth reverse logistics all start with your warehouse receiving process. Partnering with a 3PL that prioritizes excellence is a way to ensure receiving accuracy and give retailers a competitive edge.
The inbound process oftentimes doesn’t get the limelight, but in warehousing, it is often the place where games are won and lost…where cities are saved from destruction by fire…where teeth are saved from…plaque buildup? You get the point. Prevent problems from starting in the first place and you’ll be in a great position to succeed.
Ready to streamline your warehouse receiving process and reduce fulfillment errors?
Connect with a WSI expert to see how our proven receiving practices can set your operations up for success.
About the Author
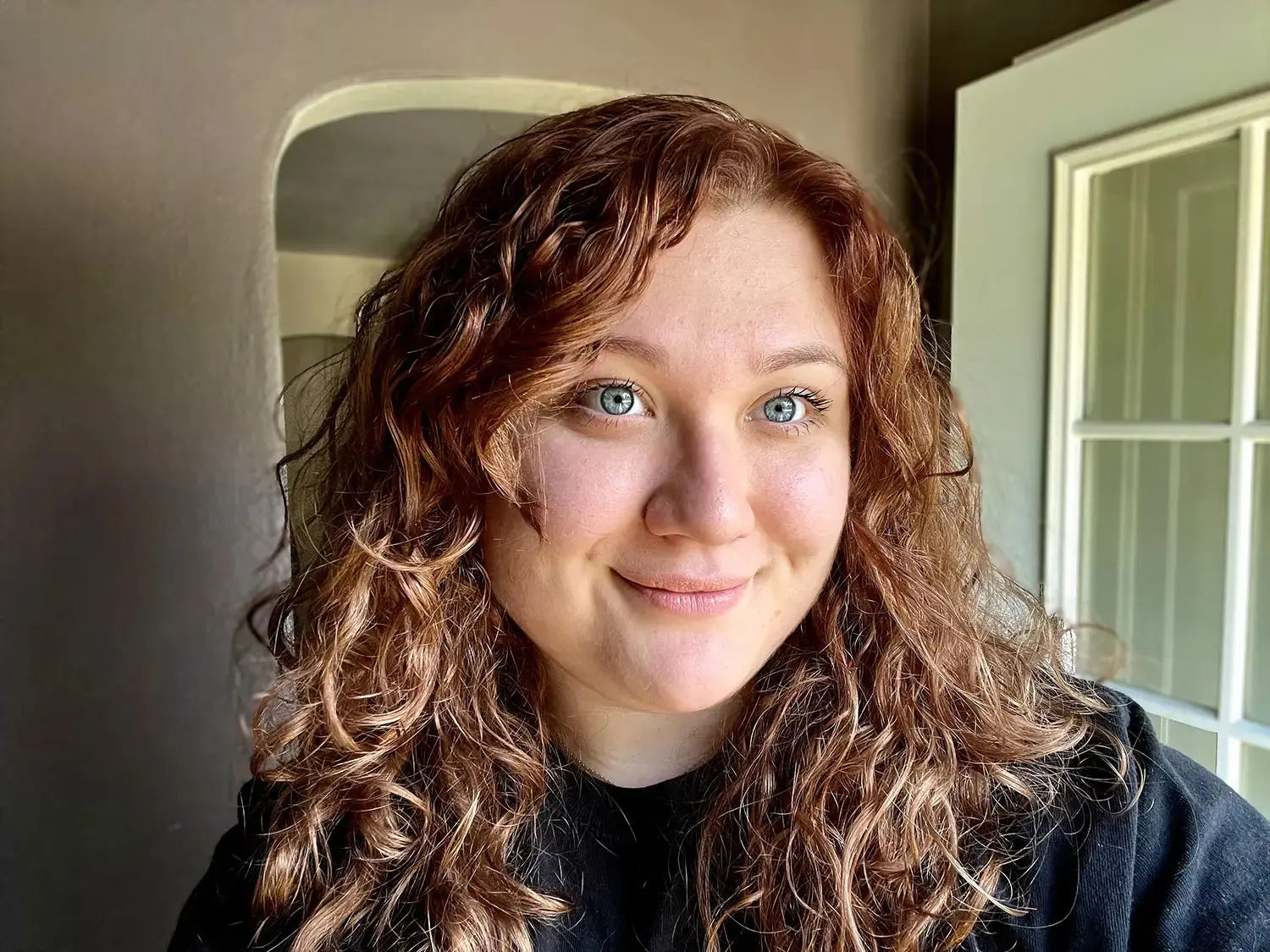
Mikayla Josefchuk
Mikayla Josefchuk is WSI’s Inside Sales and Marketing Representative, providing customers with insights on tailored supply chain solutions including warehousing, transportation, and eCommerce fulfillment. A business school graduate of the University of Missouri – Columbia, Mikayla focuses on business development and content creation. When she’s not at work, Mikayla spends her time on walks with her dog, Boone.