An Introduction to Chemical Warehousing
Chemical storage and handling require specialized knowledge and capabilities not found in other logistics operations. Chemical compounds may be explosive, hazardous to people, or dangerous to the environment, making it essential that they are stored and handled correctly to reduce risk and avoid accidents. Not all chemicals have dangerous properties, but even less volatile or relatively safe chemicals may have unique storage needs to mitigate the risk of leaks, spills, or bad reactions.
Due to the specialized nature of chemical warehousing, many chemical processing and manufacturing businesses choose to hire a third-party logistics (3PL) partner with chemical expertise to manage the storage and distribution of their products. This article will explore the complexities of chemical warehousing and some of the best practices for safe chemical storage.
CHEMICAL CLASSIFICATIONS FOR STORAGE & HANDLING
Much of the complexity of chemical logistics has to do with the various systems used to categorize chemical materials. Numerous regulatory standards apply to chemical storage and transportation to provide guidance for businesses that must store and use chemicals. Here are some of the most prominent.
OSHA HCS
To establish safe chemical storage operations first involves developing an understanding of the varying types of chemical products. The Occupational Safety and Health Administration (OSHA) has released specific guidelines in its Hazard Communication Standard (HCS) to help chemical manufacturers and chemical logistics operators clearly define the level of hazard presented by the products they work with. The HCS begins classifying hazardous chemicals by breaking them into two broad categories:
• Health hazards: A chemical may be classified as hazardous if there is sufficient scientific evidence that exposure will cause negative impacts to human health. Health hazards may range widely, from simple irritants to more severe hazards like carcinogens, corrosives, and toxins.
• Physical hazards: OSHA classifies a chemical as a physical hazard when scientific evidence suggests it is flammable, combustible, explosive, unstable, reactive with water, or oxidative, among other threats.
USDOT
The U.S. Department of Transportation (USDOT) categorizes hazardous chemicals into nine classes. Understanding these classes can help to inform appropriate storage conditions:
• Class 1: Explosives
• Class 2: Gases
• Class 3: Flammable Liquid and Combustible Liquid
• Class 4: Flammable Solid, Spontaneously Combustible, and Dangerous When Wet
• Class 5: Oxidizer and Organic Peroxide
• Class 6: Poison (Toxic) and Poison Inhalation Hazard
• Class 7: Radioactive
• Class 8: Corrosive
• Class 9: Miscellaneous
The DOT divides each of these classes further into sub-classes. A chemical’s class and subclass impacts how it must be packaged and labeled for transportation, which can directly influence where and how the product is stored in the warehouse.
Many organizations and agencies monitor and audit facilities to ensure procedures adhere to compliance standards. Chemical warehouse operations will also need to receive certification from many regulatory and transportation bodies. These organizations include the Occupational Safety and Health Administration (OSHA). OSHA provides clear regulatory guidance concerning chemical storage and transportation, such as its Hazard Communication Standard (HCS), Hazardous Waste Operations and Emergency Response (HAZWOPER) guidelines, and Safety Data Sheets (SDS).
Other organizations and regulatory bodies that may be involved are:
- U.S. Department of Transportation (DOT)
- U.S. Environmental Protection Agency (EPA)
- U.S. Department of Homeland Security (DHS)
- U.S. Customs and Border Protection (CBP) – Customs-Trade Partnership Against Terrorism (C-TPAT)
- International Maritime Organization (IMO) – International Maritime Dangerous Goods (IMDG) codes
- International Air Transport Association (IATA)

INDUSTRIES REQUIRING CHEMICAL WAREHOUSING
The chemicals manufacturing sector is vast. We normally associate this industry with pharmaceuticals, petrochemicals, and agricultural industries. Yet there are numerous other companies that work with chemicals such as:
- Welding
- Semiconductors
- Electronics
- Painting
- Jewelry-making
- Automotive
- Food
- Health care
- Plastics manufacturing
- Transportation
There are also many products that fall under chemical warehouse requirements that we do not typically consider as a chemical industry product. For example, fertilizer purchased at a home improvement store is considered a chemical product. The need for safe and secure chemical warehousing logistics is necessary to receive the right chemicals in the specified quantities without contamination.
SEPARATING CHEMICALS IN THE WAREHOUSE
In chemical warehouses, chemical products get divided and stored based on the specific threats they pose in accordance with the USDOT and OSHA guidelines above. These threats typically consist of six categories:
- Corrosives. Corrosive chemicals should be stored in a cool, dry, and well-ventilated area separate from other chemical types and other processing areas. The storage area should contain corrosion-resistant shelves, walls, and floors, and all storage containers should be exceptionally resistant to the specific chemicals stored within them.
- Explosives. Explosive chemicals range from known explosive agents to material with a very low-sensitivity explosive potential, but all must be stored in a way that mitigates their explosive risk. This includes the use of lighting and material-handling equipment that incorporates explosion-proof enclosures to avoid exposure to static electricity and sparks that pose an ignition risk.
- Flammable. All flammable solids and liquids must be stored away from other materials in a dedicated room with a fire suppression system. Depending on the material, flammable chemicals will usually be stored on a specialized racking system or within cabinets. Long-term storage may require the use of more specialized containers meant to hold flammable chemicals.
- Gases. Gaseous chemicals can vary widely in their appropriate storage methods. They may require the same requirements as flammable chemicals, explosives, toxins, or some combination of storage methods. Since most gases are stored in a compressed form, it’s essential to store them in such a way that cylinders won’t fall or be impacted by moving equipment.
- Oxidizers. Oxidizing chemicals should be stored in temperature-controlled rooms separately from any flammable or combustible materials. Oxidizer storage areas must have no windows and good ventilation as well.
- Toxins. When chemicals are toxic to humans, they must be kept in a specialized room classified for poison storage. Toxic storage rooms feature specialized ventilation that filters the air before recirculation. Chemical warehouses must also ensure that all toxic chemicals are appropriately labeled for safety and compliance purposes.
It’s essential for any chemical warehousing operation to closely follow all requirements for chemical storage. Failing to separate specific chemical types can result in explosions, fires, or other catastrophic accidents. It’s also very important to thoroughly analyze data sheets for each chemical, as chemicals within the same storage classes may still require separation from each other.
Employees at chemical storage facilities must receive undergo scheduled hazardous material training. Through this training, they learn how to appropriately handle the types of chemicals they work with, safely clean up spills, and rapidly respond to emergencies. This training is essential for compliance in any chemical logistics operation.
CHEMICAL WAREHOUSING SERVICES WITH THE EXPERTS AT WSI
The above information only scratches the surface of what it takes to safely store, handle, and ship dangerous chemical goods. Due to the specialized nature of chemical warehousing operations, many manufacturers choose to partner with a chemical logistics 3PL. An experienced 3PL that knows how to work with your chemical class can save significant money on overall logistics costs and give you peace of mind that your hazardous materials will be responsibly managed.
At WSI, our chemical sites are certified as Responsible Care partners with the American Chemistry Council, and we are a member of Operation Clean Sweep. We possess the experience, certifications, and sustainability commitments necessary to store, distribute, and transport any chemical product safely and ethically. Reliability is Everythingâ„¢.
For more information about our chemical logistics capabilities or other services, please contact us today.

About the Author
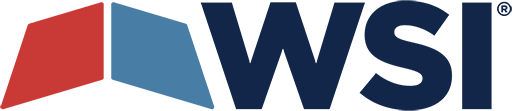
WSI Team
WSI is one of the largest privately held 3rd party logistics companies in the U.S. and spans a nationwide distribution network with global logistics reach.