Logistics Challenges in Regional Manufacturing
Tariffs, tactical economics, and geopolitical maneuvers continue to test global supply chains. The solutions necessary for enterprise survival include regional manufacturing and close-proximity suppliers, reshaping the standardized logistics infrastructure. While the shift may appear sudden, the reapportion of resources has been underway since the 2020 global pandemic.
In a recent Gartner survey, according to SupplyChainBrain, 35% of supply chain leaders reported using regionalized production, with at least two suppliers or factories, each located in different areas dedicated to regional consumption. Looking forward to 2028, the research firm forecasts that 70% of companies will integrate nearshoring within their supply chain models to boost regional network performance and maintain resiliency, despite volatility and uncertainty.
Is there a golden failproof formula or must businesses default to trial and error?
Distributed manufacturing on the move.
Regional manufacturing strategies are in the works across multiple industries. With the right tools, technology and talent, businesses can readjust and stay on track to meet customer demand. But if the logistics piece cannot accommodate or align with the transformation, success is unrealized. Without a coordinated plan from production through end-delivery, it’s a conundrum that can turn business sideways.
Many global organizations have stepped into the U.S. with regional manufacturing and logistics by building more facilities or expanding existing ones to facilitate shorter lead times, cost savings, and reach customers efficiently. Among them are retail giants Amazon, Walmart, and Nike, and Chobani, Roche, Eli Lilly, Nvidia, Hyundai, GE Aerospace, and Taiwan Semiconductor, to name a few. However, before you go headfirst into formulating a regional supply chain footprint, tread lightly by reviewing the pros and cons.
Regional manufacturing opportunities
There’s a cause and effect to integrated localized manufacturing and logistics networks. Using its advantages can facilitate stability and create a competitive edge. Here’s how.
Enhancing supply chain resilience
When manufacturers and suppliers regionalize logistics, vulnerabilities common to global networks lessen and businesses have greater control and accountability across tighter supply chains and shorter transportation routes. This increased accessibility supports reliability in sourcing, storage, and delivery of sensitive goods and materials, high-value components, and other consumer products while bypassing delays and disruptions that can occur cross-border or overseas.
Agility across demand cycles
For retailers and omnichannel businesses, seasonal product offerings and geotargeted consumer markets require inventory flexibility to meet fluctuating demand or special customization requests.
Through regional manufacturing and having localized logistics partners, businesses can make quick pivots and ensure products are available in relevant locations reducing stockouts and oversupply, optimizing warehouse space, truckloads, and route planning, improving the customer experience.
Cost efficiency and faster delivery
Closer routes bring cost savings in fuel, equipment maintenance, freight and customs fees, product handling, loading, and storage. By clipping transit times, logistics workers manage and fulfill orders in locations they’re already familiar with, boosting productivity and speed-to-market.
Sustainability and environmental benefits
People favor manufacturers and suppliers committed to sustainable practices. And because sourcing, technology, operations, and shipping bear environmental impacts, logistics companies have opportunities in lowering carbon emissions too, boosting brand reputation, customer retention, and client acquisitions, simply by reverting to a regional distributed network.
Stronger supplier and customer relationships
Supply chain resiliency is correlated to how well industry partners collaborate through transparency, visibility, and a shared vision toward solutions. Working within a regionalized manufacturing and logistics framework streamlines systems and presents untapped efficiencies benefiting partners and customers, engaging long-term relationships.
Expanding market reach
Regionalizing supply chains is a welcome strategy to open untapped markets. On a national level, manufacturers can increase product interest and introduce new goods by establishing test market areas. Companies can decipher the data, scale efficiently, and distribute products in a financially feasible manner without compromising quality control.
Regional manufacturing challenges
Opportunities that surface from localized supply chains can spur new dilemmas. Change management, workforce insecurities, and unfamiliar regulations increase operational complexities. Novice logistics providers find the learning process peppered with obstacles but knowing what to expect can help avert miscalculations and achieve transformative results.
Supply chain fragmentation and increased complexity
Going from centralized distribution centers to a regionalized approach, at first, can seem disjointed and upend the supply chain’s big picture. Instead, a localized manufacturing, supplier, and logistics network helps businesses fine tune product offerings and inventory management, meeting customers where they are, both figuratively and literally, presenting more robust yet succinct economies of scale.
The number of distributed network participants grows by providing businesses with more options, but system integration challenges can disrupt fulfillment and the movement of goods. However, with strong supplier relationships, collaborative-friendly digital integration, and continuous improvements across warehouse facilities, the benefits of regional supply chains supersede the risks.
Increased transportation costs and infrastructure variability
Compressed logistics routes reduce transportation costs but there are other expenses to consider in short hauls. Regional manufacturers must cast a wider localized mix of transit partners to meet order volume and last-mile delivery expectations.
More providers can increase competition and create pricing swings. Well-intended route modifications and shifts in distribution hubs can inadvertently offset cost and time efficiencies. Road conditions and neglected transportation infrastructure can lead to accessibility issues, delays, and losses.
Without conducting due diligence, businesses can find themselves unaware of new logistics requirements and ill-prepared to adapt. Once logistics gaps are discovered, expenses incurred to remediate the shortfall can consume the original cost savings sought.
Regulatory and compliance challenges
Global supply chains are adept at embracing geographical, cultural, and regulatory differences, a mainstay of doing business in multiple countries. Organizations looking to sidestep those complexities restructure third-party alliances by working in regional networks, and may be surprised with new demands.
State-to-state, cross-border, and onshoring trade relations have their own regulatory frameworks which may not coincide. Varying tax and labor laws, environmental standards, and social governance guidelines impact manufacturing, supplier, fulfillment and logistics costs, impacting workers and customers.
For example, companies may need to invest in technology systems that can set, track, and modify labeling and packing to remain compliant within localized shipping and distribution regions to avoid fees, penalties, and delays.
Is a DIY regional logistics solution a possibility
Opting for regional manufacturing and localized distributed networks adds a learning curve to operations. Strategic partnerships, meant to streamline each aspect of the sale-to-delivery funnel, can hamper efficiency: more touchpoints in supply chain systems minimize control.
Organizations could gain command of their business by handling their own regional logistics. But do-it-yourself (DIY) endeavors require deep pockets, unwavering conviction, and staying open to constructive criticism. Here’s why.
Do-it-yourself could be cost-prohibitive
To do logistics well requires having a thorough understanding of the capital investments needed to set up a successful operation, as well as maintaining and updating those investments to stay competitive and compliant. Depending on the products involved and where they are stored, handled, and shipped, costs can escalate, sometimes without warning. Here’s how:
- The structure: Where operations happen, whether the building is owned or leased, can be expensive. Annual costs can reach $200,000 or more, depending on square footage, specialized conditions (temperature-cooled or sustainable construction), and region. Ensuring products are stacked, stored, handled, and packed safely and securely shows a commitment to duty of care.Warehouse equipment, such as forklifts, stackers, pallets, shelving, lift tables, stretch wrappers and more supports that objective. Warehousing equipment can typically involve a $40,000 to $150,000 investment, plus another $80,000 to $300,000 to cover recruitment expenses, new hire salaries, and payroll.
- The fleet: Product demand, volumes, weight, and distance to ship play a role in the type of trucks needed. Purchasing (or leasing) a fleet can run $100,000 to $500,000, excluding depreciation which further erodes the value over time. New and used vehicles require ongoing safety inspections, maintenance checks and repairs, adding 15% to the acquisition costs. Don’t forget to include insurance, fuel surcharges, and tolls, adding another 10% to logistics startup costs.
- The systems: Achieving cost efficiency across multiple companies within the same regional manufacturing and distribution network seldom happens without the use of integrated systems monitoring product selection, location, and delivery. Logistics providers rely on Transportation Management Software (TMS) and Inventory Management Systems (IMS) as sources of truth, where data gathering and reporting meet product tracking, accountability, and compliance in real time for greater accuracy and cost savings from point of origin to last mile delivery. TMS, IMS and other technologies make up the logistics IT infrastructure, essential to reducing cyber intrusion and security risks, at a starting price of $30,000. Regional logistics providers also need to obtain licenses, legal permits, and business insurance to operate in good standing: $10,000 to $50,000 out the gate
- The marketing: Investing in the right tools, technology, and talent is important but it won’t bring in business unless customers, industry peers, and ancillary businesses know you exist. Online, offline, and word of mouth marketing campaigns help establish a brand, share the value proposition, and generate interest in different regions by succinctly targeting audiences, a likely $20,000 to $100,000 investment. The total logistics start up investment is a hefty chunk of change; six to seven figures, but there’s more.
DIY logistics takes an investment in time
With diverse regulatory and compliance requirements constantly evolving, ensuring they align with differing local, state, and regional laws can be a handful for businesses looking into regional manufacturing and logistics. Understanding the information and knowing how to apply it takes time. As you build a logistics network of your own or partner with a third-party, strategies change to match determined objectives.
Keeping a pulse on industry changes helps:
- minimize risks
- maintain compliance
- provide education and training
- product and service offerings stay relevant
- protect long-term business investments, and
- upholds company integrity.
Now that we’ve uncovered the logistics challenges to regional manufacturers and suppliers, how can national and localized supply chains work collectively to manage complex logistics networks?
Adaptability is a strategy
There’s no reason to overextend business obligations when a matrix of diverse talent and reliable logistics organizations are ready to support regional markets. Part of operational course correcting includes route planning, demand forecasting, and scalability adjustments to fit a regional logistics framework.
The beauty of working within a diversified network of logistics providers allows you to: 1) leverage their technology, 2) collaborate with experts, and 3) deploy smart, equitable, integrated supply chain systems so every partner benefits.
Optimizing regional logistics
Regional manufacturers transporting materials directly to customers can engage next-level efficiency with cross-docking, consolidating shipments for faster delivery.
For longer routes or multiple stops within a U.S. region, multi-modal transportation options offer flexibility and cost-savings while supporting the environment. By combining rail warehousing and transit with truck hauls, manufacturers can tailor inventory holds, storage, routes and delivery, balancing customer needs and efficiency.
Regional logistics solutions, supported by technology integration and real-time visibility, add more value to today’s strategic relationships. With economic and trade environments relying on regulatory adherence, a 3PL that puts award-winning compliance standards to work across many regions presents a golden opportunity for manufacturers.
The right 3PL partner for redistributed manufacturing (RDM)
If you’re a manufacturer or supplier modifying logistic strategies and ramping up regional infrastructures, make sure your next transportation and warehousing partner can offer:
- Multi-regional capabilities with specialized expertise
- Established compliance and regulatory knowledge
- Technology integration and real-time visibility tools
- Scalability through regional expansion
- Versatility to meet evolving demand
- A skilled, trained, and reliable workforce
Or take the shortest route and call WSI. We’ll help you explore the benefits of working with our wide network of supply chain professionals specializing in regional fulfillment and logistics. Let us be a part of your regional manufacturing operations.
About the Author
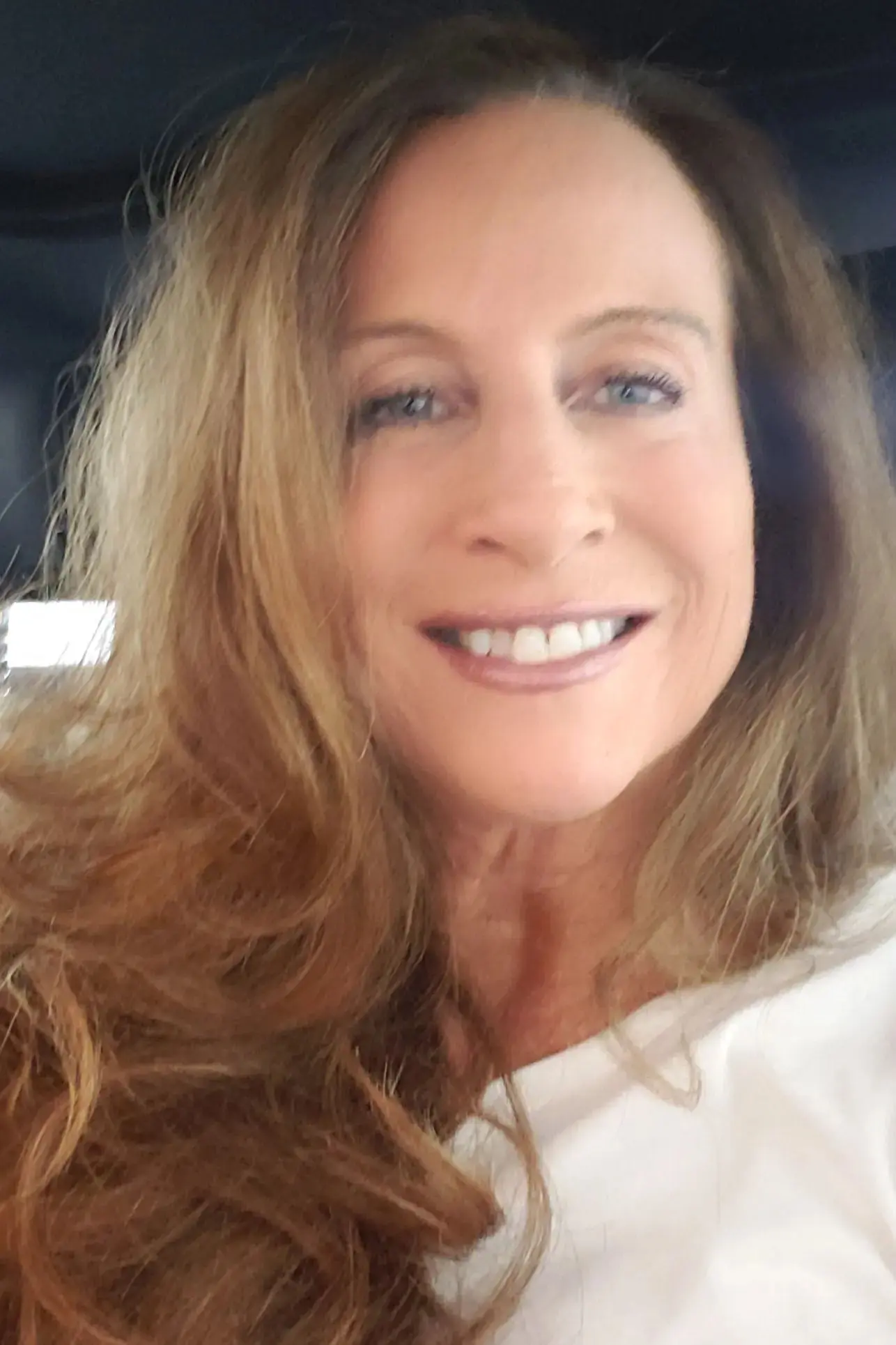
Melanie Stern
Melanie enjoys a longstanding career in communications, crafting content for varied industries. Her experience includes writing blogs, news editorial, feature articles, social, and broadcast segments. She also hosts Institute for Supply Management’s bi-weekly podcast “Supply Chain – Unfiltered”.