Chemical Logistics: Why Chemical Companies Are Rethinking Their 3PL Partnerships
In a recent Inbound Logistics article about chemical logistics, transportation, and storage, the industry’s main pain points were brought to light. As a leader in the chemical logistics space, WSI was featured for its deep understanding of the rising demands, complexities, and risks involved in the chemical supply chain.
If there’s one key point chemical companies can walk away from the article with, it’s how critical the right 3PL partner is. With growing scrutiny on 3PLs that handle and store chemicals, it’s clear that a partner without experience becomes a liability, breeding risk rather than resilience. And that’s because, in this environment, basic compliance isn’t enough; true chemical logistics excellence is essential.
What’s driving chemical companies to reevaluate their 3PL partners?
Chemical companies face new logistics pressures, from increased regulations to labor shortages. Without the proper operational infrastructure in place to handle disruptions, compliance, and create operational efficiency and cost-effectiveness, chemical companies may find themselves struggling to create a safe, agile, and resilient chemical supply chain.
Some of the top challenges facing the chemical industry include:
- Increased regulation: The number of regulations surrounding chemical logistics is growing, both in the US and globally. For example, OSHA has increased the number of warehouse audits and companies must adhere to Clean Air Acts, lower emissions standards, and sustainability directives from the EU and Canada.
- Labor market volatility: Inbound Logistics’s article highlighted a “tight labor market” within chemical logistics. One featured area was driver shortages, and the need for drivers who were skilled in regulations and the processes surrounding chemical transportation. In addition, the industry is experiencing turnover and retraining challenges. The hope is to raise wages to attract more workers and leverage technology to provide more visibility and cost-effectiveness in the chemical supply chain.
- Supply chain disruption: Supply chain disruptions have become somewhat of a norm. Whether it’s geopolitical instability, extreme weather, port strikes, or some other factor that creates a “butterfly effect,” retailers have learned the importance of becoming agile and resilient in the face of ongoing supply chain challenges.
- Cost containment: During the pandemic, speed often took precedence, with companies paying premiums for on-time delivery. However, over the past year, for chemical companies, the pressure to contain costs while maintaining reliability has grown. The culmination of market volatility, labor shortages, and inflation has shifted focus to operational efficiency and long-term savings. With the added pressure of rising transportation rates, increased regulatory costs, and shifting modal preferences (e.g., from truck to rail), chemical logistics leaders are looking for 3PL partners that can deliver more cost-effective solutions and services without compromising safety and compliance.
- Cyber and cargo threats: Between cybercrime and cargo theft, supply chains have experienced an increase in attacks on logistics infrastructure. This has created the need for real-time monitoring systems, more rigorous carrier vetting, and the implementation of stricter cybersecurity protocols and access controls.
When a 3PL partner lacks the resources, tools, and expertise to mitigate the increasing challenges and risk, chemical companies need to seek providers that have the safety, compliance, and chemical logistics know-how; it makes all the difference in developing a resilient and smooth chemical supply chain.
What chemical logistics excellence looks like
Excellence begins behind the scenes and goes beyond basic compliance. It’s about ensuring the safest environment while maximizing efficiency through modern strategies and expertise. Companies should look at chemical logistics partners that use tactics such as:
Redundant safety protocols
In certain industries, redundancy means that if one system fails, another takes over. In chemical logistics, redundancy safety protocols come in many different forms. For example, to backup systems and equipment, think of duplicate sensors or valves. For chemical transportation, it’s having alternative routes. Another redundancy is additional chemical storage facilities. 3PL partners with the right redundancy protocols in place have backups prepped and ready to maintain efficiency and mitigate risk.
Other redundancy protocols include:
- Functional redundancy – Having multiple safety systems in place to address the same hazard, for example, combining automated sprinklers with gas-based fire suppression. It also includes backup power sources, such as generators, to ensure critical systems stay operational during outages.
- Human redundancy – Training employees to manually shut down processes if automated safety systems fail.
- Packaging and handling redundancy – To increase transport safety, develop multiple layers of protection, like secondary containment and using UN-certified packaging. Implement emergency preparedness that ensures swift and effective responses if an incident occurs.
Proactive inspections
Think about it: When is the business that “meets expectations” chosen over the one that “exceeds expectations.” 3PL partners that go beyond regulatory minimums to catch issues before they become hazards are the providers chemical companies should look for. This means they participate in routine equipment checks, atmospheric monitoring, and verifying that all safety systems are fully operational.
Another way partners can be proactive is through dedicated regulatory expertise. These are the people who stay on top of shifting rules that span multiple agencies. When in-house compliance is part of a 3PL’s operations, it ensures that chemical logistics operations stay up to date with evolving standards. These teams also maintain audit-ready documentation and provide proactive consultation to help clients navigate complex requirements with confidence.
Specialized infrastructure
Chemical storage requires more than standard warehousing. Chemical warehousing needs specialized environments designed for safety and precision. Businesses should look for 3PL providers with facilities equipped with containment zones, temperature control, and bulk liquid handling capabilities. These environments help prevent cross-contamination and environmental hazards, maintain product integrity for sensitive materials, and support transfers of hazardous or high-volume materials.
Integrated technology
A modern supply chain tech stack is not only for more common fulfillment operations but imperative for specialized logistics as well. Technology can elevate chemical warehousing and logistics from reactive to proactive by using solutions such as automation, a transportation management system (TMS), and predictive analytics. This helps by:
- Automation: Reducing manual errors and increasing operational efficiency.
- TMS: Providing end-to-end visibility, enabling real-time tracking, dynamic planning, and accurate reporting.
- Predictive analytics: Identifying and addressing potential risks before they escalate.
Cyber and cargo risk management
With the threats to today’s supply chain, chemical companies need partners that prioritize risk mitigation. Common strategies include real-time cargo and systems monitoring to detect issues early and take fraud prevention measures, like verifying safety ratings and credentials.
Chemical logistics excellence is based on a system built through culture, infrastructure, processes, and people. It’s crucial for chemical companies to seek excellence in their partners, especially at a time when the stakes are high.
The WSI proof in practice
WSI doesn’t just comply; we lead with operational excellence, reducing risk while enabling sustainable growth. The results: lower costs, fewer errors, and scalable operations without compromising safety.
Case study: Managing complex chemical logistics
A top US producer of advanced polymers and high-performance plastics turned to WSI to overcome rising shipping errors, inefficiencies, and inflated logistics costs. With a vision centered on innovation and sustainability, the company needed a 3PL partner with deep chemical expertise, flexible solutions, and shared values.
WSI delivered with a tailored, hybrid model combining dedicated and multi-tenant chemical facilities, supported by expert teams trained in HAZWOPER, IMDG, IATA, and DOT standards. The partnership now spans nearly 3 million square feet and includes services like bulk transfers, blending, and spill mitigation, plus cost-saving innovations like on-site yard spotting and flexible financing.
Thanks to WSI’s operational excellence and environmental commitment, including Responsible Care® certification and participation in Operation Clean Sweep, the relationship continues to thrive, proving that when safety, sustainability, and performance align, growth follows.
Read the full case study here.
A partner that’s built for what’s next
The chemical industry is changing fast, and only logistics partners with the infrastructure, expertise, and foresight can keep up. WSI has an unmatched commitment to safety, compliance, and tailored service. As the first 3PL certified as a Responsible Care® Partner, WSI goes beyond regulatory requirements with specialized infrastructure, temperature-controlled environments, and expert handling of hazardous materials. With a full suite of services from blending and packaging to bulk transfers and transportation, WSI offers scalable, end-to-end solutions trusted by global leaders in petrochemicals, plastics, and specialty chemicals. Contact our team today to partner with a 3PL built to handle today’s risks and tomorrow’s growth.
About the Author
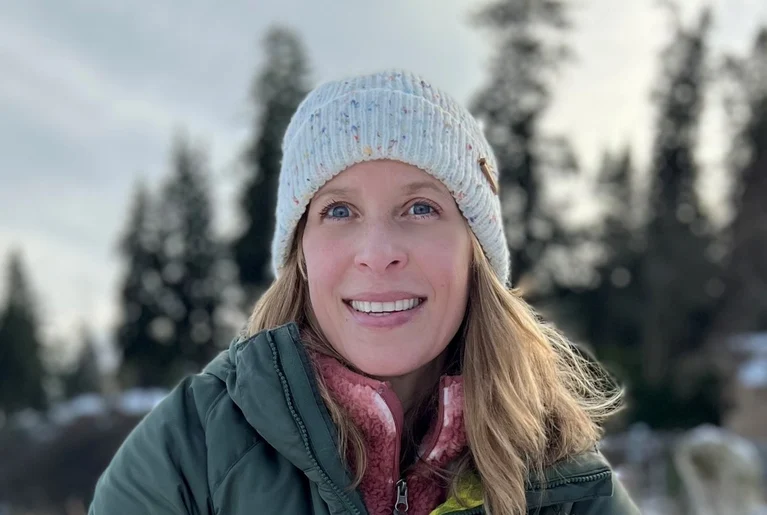
Alyssa Wolfe
Alyssa Wolfe is a content strategist, storyteller, and creative and content lead with over a decade of experience shaping brand narratives across industries including retail, travel, logistics, fintech, SaaS, B2C, and B2B services. She specializes in turning complex ideas into clear, human-centered content that connects, informs, and inspires. With a background in journalism, marketing, and digital strategy, Alyssa brings a sharp editorial eye and a collaborative spirit to every project. Her work spans thought leadership, executive ghostwriting, brand messaging, and educational content—all grounded in a deep understanding of audience needs and business goals. Alyssa is passionate about the power of language to drive clarity and change, and she believes the best content not only tells a story, but builds trust and sparks action.